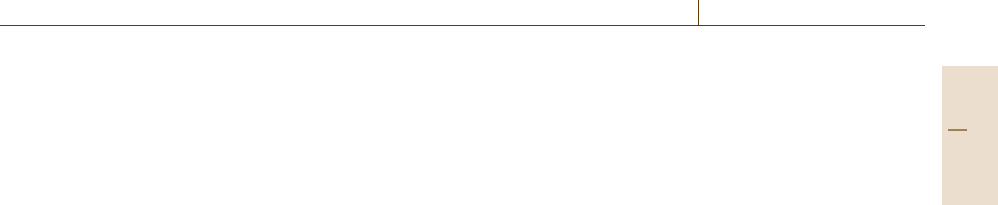
Mechanical Properties 7.6 Permeation and Diffusion 431
sorbing penetrants in rubbery or glassy polymers
often swell the polymer at sufficiently high activ-
ity, leading to changes in polymer properties (e.g.,
glass-transition temperature, fractional free volume,
etc.) and penetrant diffusion coefficients [7.264].
Frisch developed an explicit expression for the time
lag when the diffusion coefficient is concentration-
dependent [7.283]. Crank treated this subject in detail
using both analytical and numerical methods [7.261].
Strictly speaking, most of these treatments require
knowledge of the functional form of the relation-
ship between diffusion coefficient and concentra-
tion [7.261]. In contrast, the steady-state measure-
ments discussed in Sect. 7.6.1 can provide a reliable
way to evaluate diffusion, solubility and permeability
coefficients without making a priori assumptions re-
garding the concentration dependence of the diffusion
coefficient.
Various experimental approaches have been re-
ported to measure gas transport through polymeric
films. In principle, most of the techniques directly mea-
sure gas flux through the film or gas uptake by the
film (i. e., solubility). Diffusion coefficients are typi-
cally derived indirectly from permeability and solubility
measurements based on the theory introduced earlier. In
the following sections, general strategies are described
for measuring gas transport properties in polymers.
7.6.3 Experimental Measurement
of Permeability
Film Preparation
The measurement of gas flux requires the success-
ful preparation of a uniform, nonporous thin film. In
general, polymer films for permeation testing have
thicknesses of less than 250 μm, unless special situa-
tions require a thicker film. For example, thicker films
may make it easier to prepare nonporous specimens
for study, or they may be used to increase the time
lag when studying penetrants with high diffusion co-
efficients (e.g., He or H
2
). Uniformity of thickness is
important for reducing the uncertainty in permeability,
as illustrated in (7.124). A nonporous film is required
if one wishes to determine the inherent properties of
the material under study, because gas flow through
a pinhole obeying Knudsen diffusion can be orders of
magnitude faster than that through a dense film obeying
the solution–diffusion mechanism [7.258]. Thus, any
pinhole defects in a sample can compromise the accu-
rate measurement of gas flux through a polymer film.
The first challenge in successfully measuring gas per-
meation properties typically lies in the ability to prepare
uniform, pinhole-free films.
Polymer films are typically prepared in the labora-
tory by melt-pressing and solvent-casting [7.284, 285].
Melt-pressing is used less often than solvent-casting
to prepare films for study. In melt-pressing, one ap-
plies heat to melt a polymer powder, and then a film is
made by pressing the molten polymer under high pres-
sure. Solvent-casting is a widely used method to prepare
films. In this method, solid polymer is dissolved in a sol-
vent, the resulting solution is cast on a leveled support,
and the solvent is allowed to evaporate slowly, leaving
a solid film behind.
Gas permeation properties of films are often influ-
enced by many processing factors. One critical factor
is the solvent used in preparing the film, which can
strongly affect polymer morphology and, in turn, gas
permeation properties. For example, poly(4-methyl-1-
pentene) films were prepared by solvent-casting using
chloroform and carbon tetrachloride [7.285]. The N
2
permeability at 35
◦
C and 2 atm is 1.1 Barrers for
a film prepared from chloroform solution, but it is
6.0 Barrers for a similar film prepared from carbon
tetrachloride solution, even though the two films ex-
hibit almost the same crystallinity values (i. e., 57%
and 56%, respectively) [7.285]. Other possible factors
influencing gas transport properties include polymer
concentration, evaporation temperature, annealing con-
ditions, etc. Pinholes in a solid film can be introduced
during the solvent-casting process by bubbles present
in the solution before casting, the presence of insoluble
impurities in the solution (such as dust), and very rapid
solvent evaporation. Typically, before casting, the solu-
tion is filtered to remove any impurities, and the solvent
evaporation rate is controlled during film drying. For
highly crystalline polymers such as poly(ethylene ox-
ide), thermal annealing above the melting temperature
could be critical to form defect-free films, although the
reason for this is not clear [7.275].
Uniform thickness films can be obtained by spread-
ing the solution onto a support using tools such as
a Gardner knife or a doctor blade, which controls the
liquid film thickness [7.284]. Alternatively, the solution
may be poured into a glass ring resting on a flat solid
support. The glass ring is typically stuck to the sup-
port using silicon caulk to achieve a leak-free boundary.
The film thickness is controlled by the amount of liquid
solution added and its concentration. The solid support
needs to be leveled to obtain films of uniform thickness.
The choice of the support material can be important. If
the solution cannot wet the support, the liquid polymer
Part C 7.6