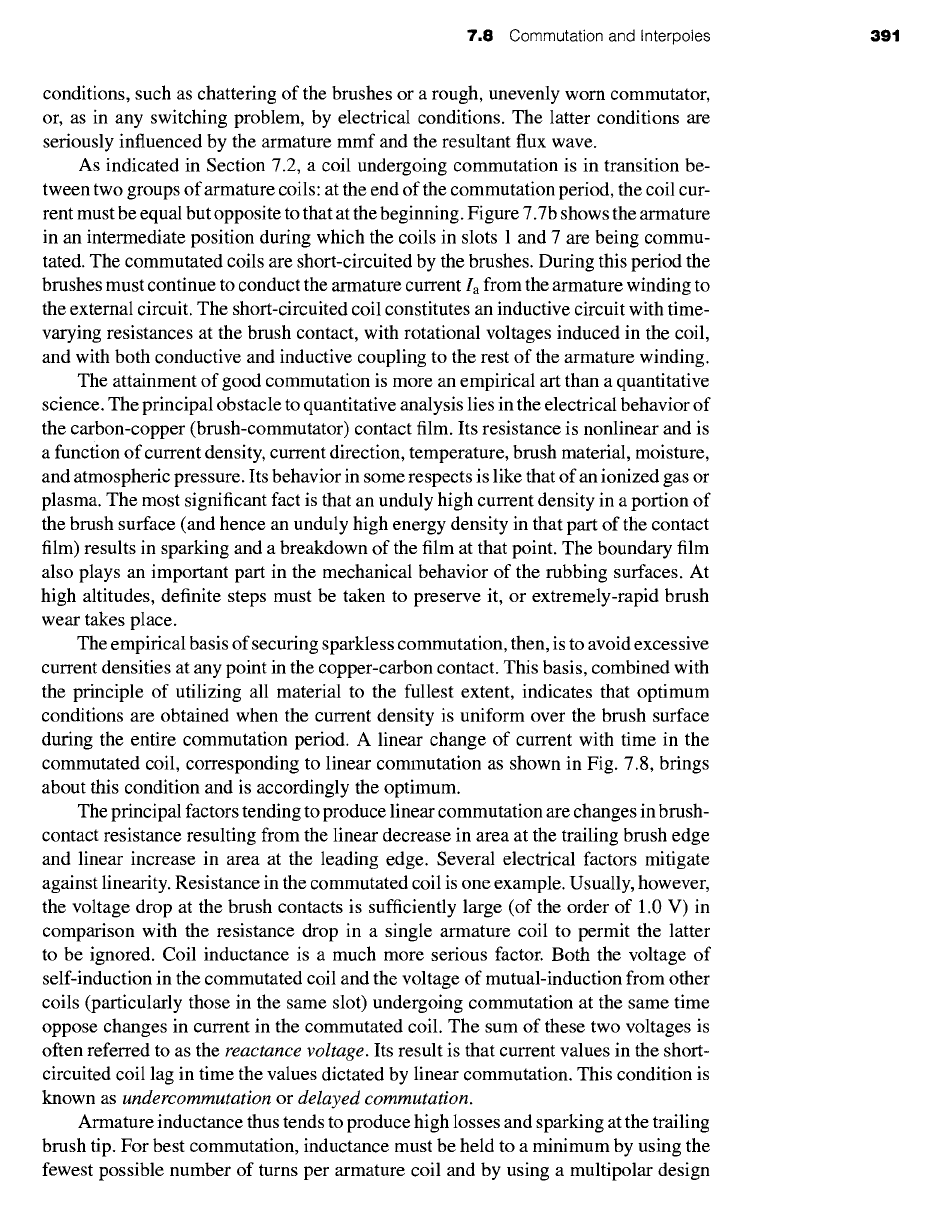
7,8 Commutation and Interpoles 39t
conditions, such as chattering of the brushes or a rough, unevenly worn commutator,
or, as in any switching problem, by electrical conditions. The latter conditions are
seriously influenced by the armature mmf and the resultant flux wave.
As indicated in Section 7.2, a coil undergoing commutation is in transition be-
tween two groups of armature coils: at the end of the commutation period, the coil cur-
rent must be equal but opposite to that at the beginning. Figure 7.7b shows the armature
in an intermediate position during which the coils in slots 1 and 7 are being commu-
tated. The commutated coils are short-circuited by the brushes. During this period the
brushes must continue to conduct the armature current Ia from the armature winding to
the external circuit. The short-circuited coil constitutes an inductive circuit with time-
varying resistances at the brush contact, with rotational voltages induced in the coil,
and with both conductive and inductive coupling to the rest of the armature winding.
The attainment of good commutation is more an empirical art than a quantitative
science. The principal obstacle to quantitative analysis lies in the electrical behavior of
the carbon-copper (brush-commutator) contact film. Its resistance is nonlinear and is
a function of current density, current direction, temperature, brush material, moisture,
and atmospheric pressure. Its behavior in some respects is like that of an ionized gas or
plasma. The most significant fact is that an unduly high current density in a portion of
the brush surface (and hence an unduly high energy density in that part of the contact
film) results in sparking and a breakdown of the film at that point. The boundary film
also plays an important part in the mechanical behavior of the rubbing surfaces. At
high altitudes, definite steps must be taken to preserve it, or extremely-rapid brush
wear takes place.
The empirical basis of securing sparkless commutation, then, is to avoid excessive
current densities at any point in the copper-carbon contact. This basis, combined with
the principle of utilizing all material to the fullest extent, indicates that optimum
conditions are obtained when the current density is uniform over the brush surface
during the entire commutation period. A linear change of current with time in the
commutated coil, corresponding to linear commutation as shown in Fig. 7.8, brings
about this condition and is accordingly the optimum.
The principal factors tending to produce linear commutation are changes in brush-
contact resistance resulting from the linear decrease in area at the trailing brush edge
and linear increase in area at the leading edge. Several electrical factors mitigate
against linearity. Resistance in the commutated coil is one example. Usually, however,
the voltage drop at the brush contacts is sufficiently large (of the order of 1.0 V) in
comparison with the resistance drop in a single armature coil to permit the latter
to be ignored. Coil inductance is a much more serious factor. Both the voltage of
self-induction in the commutated coil and the voltage of mutual-induction from other
coils (particularly those in the same slot) undergoing commutation at the same time
oppose changes in current in the commutated coil. The sum of these two voltages is
often referred to as the
reactance voltage.
Its result is that current values in the short-
circuited coil lag in time the values dictated by linear commutation. This condition is
known as
undercommutation
or
delayed commutation.
Armature inductance thus tends to produce high losses and sparking at the trailing
brush tip. For best commutation, inductance must be held to a minimum by using the
fewest possible number of turns per armature coil and by using a multipolar design