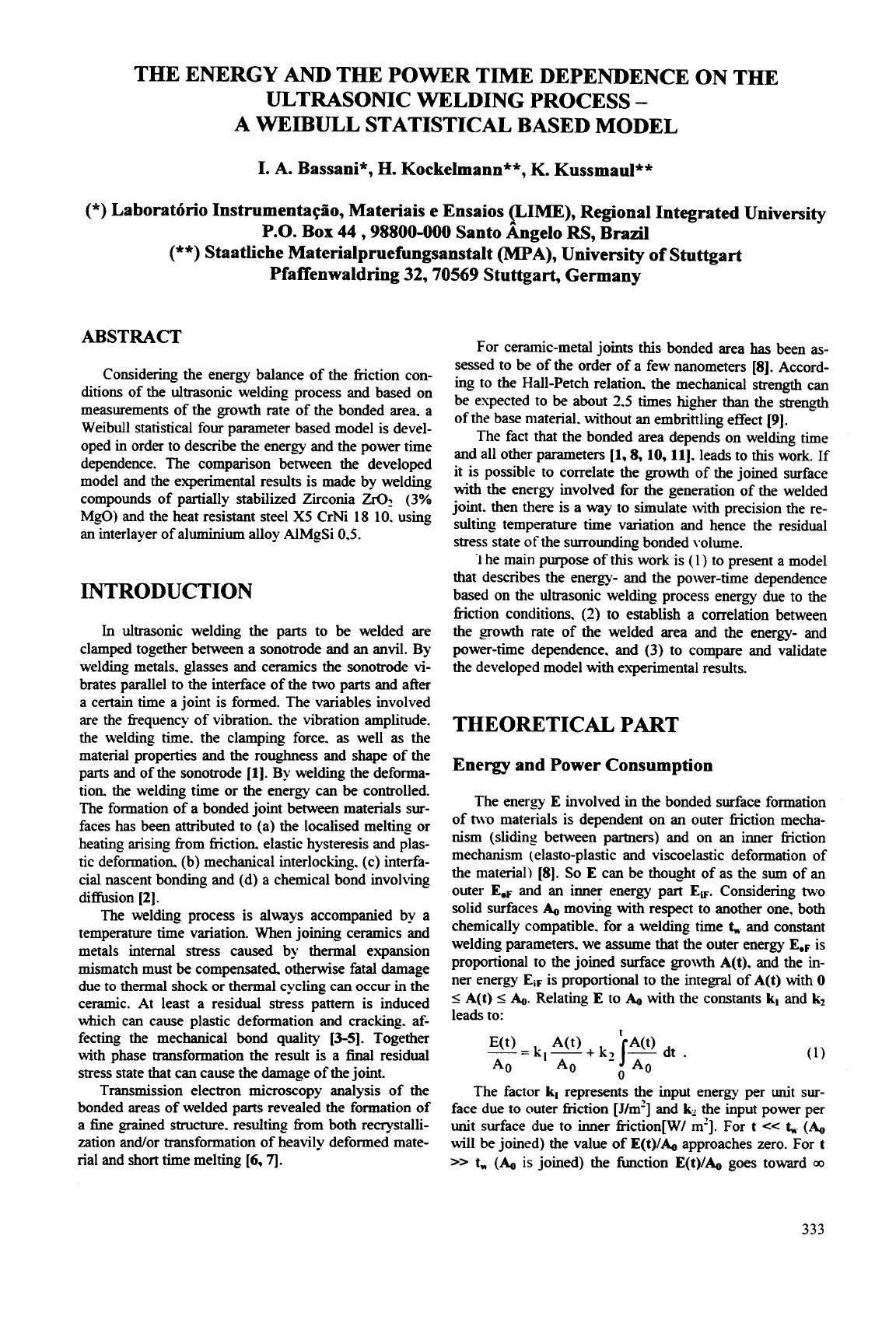
THE ENERGY
AND
THE POWER TIME DEPENDENCE
ON
THE
A WEIBULL STATISTICAL BASED MODEL
ULTRASONIC WELDING PROCESS
-
I.
A.
Bassani",
H.
Kockelmann"",
K.
Kussmaul**
(*)
Laboratbrio Instrumentagio, Materiais e Ensaios (LIME), Regional Integrated University
P.O. Box
44,98800-000
Santo hgelo
Rs,
Brazil
(**)
Staatliche
Materialpruefungsanstalt
(MPA),
University
of
Stuttgart
Pfaffenwaldring
32,70569
Stuttgart, Germany
ABSTRACT
Considering the energy balance of the fiiction con-
ditions of the ultrasonic welding process and based on
measurements of the
growth
rate of the bonded area. a
Weibull statistical four parameter based model is devel-
oped in order to describe the energy and the power time
dependence. The comparison between the developed
model and the experimental results is made by welding
compounds of partially stabilized Zirconia
zIo2
(3%
M,@)
and the heat resistant steel
X5
CrNi
18
10.
using
an interlayer of aluminium alloy AlMgSi
0.5.
INTRODUCTION
In
ultrasonic welding the parts to
be
welded are
clamped together between a sonotrode and an anvil. By
welding metals, glasses and ceramics the sonotrode
vi-
brates parallel to the interface of the two parts and after
a
certain time a joint is formed. The variables involved
are the fiequency of vibration. the vibration amplitude.
the welding time. the clamping force.
as
well
as
the
material properties and the roughness and shape
of
the
parts and of the sonotrode
111.
By welding the deforma-
tion. the welding time or the energy can be controlled.
The formation of a bonded joint between materials sur-
faces has been attributed to (a) the localised melting or
heating arising fiom fiiction. elastic hysteresis and plas-
tic deformation. (b) mechanical interlocking. (c) interfa-
cial nascent bonding and (d) a chemical bond involving
diffusion [2].
The welding process is always accompanied by a
temperature time variation. When joining ceramics and
metals internal stress caused by thermal
expansion
mismatch must be compensated. otherwise fatal damage
due to thermal shock or thermal cycling can occur in the
ceramic. At least a residual stress pattern is induced
which can cause plastic deformation and cracking. af-
fecting the mechanical bond quality [3-51. Together
with phase transformation the result
is
a
final
residual
stress state that can cause the damage of the joint.
Transmission electron microscopy analysis of the
bonded areas of welded parts revealed the formation
of
a fine ,pined structure. resulting fiom both recrystalli-
zation and/or transformation of heavily deformed mate-
rial and short time melting
[a,
7.
For ceramic-metal joints
this
bonded area
has
been as-
sessed to be of the order of a few nanometers [S]. Accord-
ing to the Hall-Perch relation. the mechanical strength can
be expected to be about
2.5
times higher
than
the strength
of the base material. without an embrittling effect [9].
The fact that the bonded area depends on welding time
and all other parameters [l, 8,10,11]. leads to
this
work. If
it is possible to correlate the
growth
of the joined surface
with the energy involved for the generation of the welded
joint. then there is
a
way to simulate with precision the re-
sulting temperature time variation and hence the residual
stress state ofthe surrounding bonded volume.
i
he main purpose of this work is
(1)
to present a model
that describes the energy- and the power-time dependence
based on the ultrasonic welding process energy due to the
fiction conditions.
(2)
to establish a correlation between
the
growth
rate of the welded area and the energy- and
power-time dependence. and
(3)
to compare and validate
the developed model with experimental results.
THEORETICAL PART
Energy and Power Consumption
The enera
E
involved in the bonded surface formation
of
hvo
materials is dependent on an outer fiiction mecha-
nism (sliding between pamers) and on an inner fiiction
mechanism (elasto-plastic and viscoelastic deformation of
the material) [S].
So
E
can be thought
of
as the
sum
of
an
outer
E.F
and an inner energy part
EI.
Considering
two
solid surfaces
A,,
mo&g with respect to another one, both
chemically compatible. for a welding time
t,,
and constant
welding parameters. we assume that the outer energy
E.F
is
proportional to the joined surface
growth
A(t),
and the in-
ner energy
EiF
is proportional to the integral of
A(t)
with
0
I
A(t)
I
A,,.
Relating
E
to
A,,
with the constants
kl
and
k2
leads to:
The factor
k,
represents the input energy per unit sur-
face due to outer fiiction [J/m'] and
k2
the input power per
unit surface due to inner fiction[W/
m'].
For
t
<<
t,,
(A,,
will be joined) the value of
E(t)/A,,
approaches zero. For
t
>>
t,,
(A,,
is joined) the function
E(t)/&
goes toward
a,
333