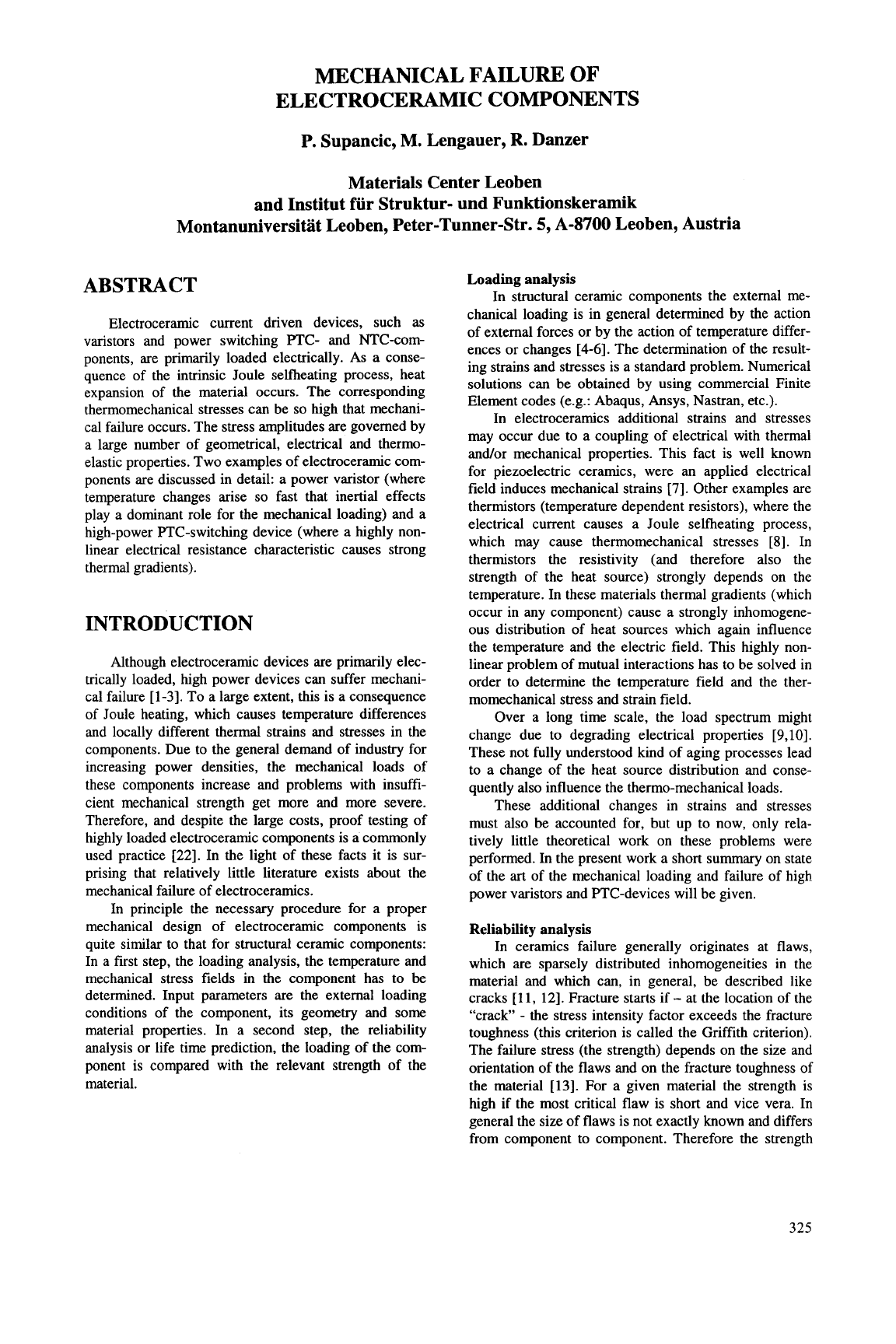
MECHANICAL FAILURE OF
ELECTROCERAMIC COMPONENTS
P. Supancic, M. Lengauer,
R.
Danzer
Materials Center Leoben
and Institut fur Struktur- und Funktionskeramik
Montanuniversitat Leoben, Peter-Tunner-Str.
5,
A-8700 Leoben, Austria
ABSTRACT
Electroceramic current driven devices, such
as
varistors and power switching PTC- and NTC-com-
ponents, are primarily loaded electrically.
As
a
conse-
quence of the intrinsic Joule selfheating process, heat
expansion of the material occurs. The corresponding
thermomechanical stresses can be
so
high that mechani-
cal failure occurs. The stress amplitudes are governed by
a large number of geometrical, electrical and thermo-
elastic properties. Two examples of electroceramic com-
ponents are discussed in detail: a power varistor (where
temperature changes arise
so
fast that inertial effects
play a dominant role for the mechanical loading) and a
high-power PTC-switching device (where a highly non-
linear electrical resistance characteristic causes strong
thermal gradients).
INTRODUCTION
Although electroceramic devices are primarily elec-
trically loaded, high power devices can suffer mechani-
cal failure [l-31. To a large extent, this is
a
consequence
of Joule heating, which causes temperature differences
and locally different thermal strains and stresses in the
components. Due to the general demand of industry for
increasing power densities, the mechanical loads of
these components increase and problems with insuffi-
cient mechanical strength get more and more severe.
Therefore, and despite the large costs, proof testing of
highly loaded electroceramic components is
a
commonly
used practice [22]. In the light of these facts it is sur-
prising that relatively little literature exists about the
mechanical failure of electroceramics.
In principle the necessary procedure for a proper
mechanical design of electroceramic components is
quite similar to that for structural ceramic components:
In a first step, the loading analysis, the temperature and
mechanical stress fields in the component has to be
determined. Input parameters are the external loading
conditions of the component, its geometry and some
material properties. In a second step, the reliability
analysis
or
life time prediction, the loading of the com-
ponent
is
compared with the relevant strength
of
the
material.
Loading analysis
In structural ceramic components the external me-
chanical loading
is
in general determined by the action
of external forces
or
by the action of temperature differ-
ences
or
changes [4-61. The determination of the result-
ing strains and stresses is a standard problem. Numerical
solutions can be obtained by using commercial Finite
Element codes (e.g.: Abaqus, Ansys, Nastran, etc.).
In electroceramics additional strains and stresses
may occur due to a coupling of electrical with thermal
andor
mechanical properties. This fact is well
known
for piezoelectric ceramics, were an applied electrical
field induces mechanical strains
[7].
Other examples are
thermistors (temperature dependent resistors), where the
electrical current causes a Joule selfheating process,
which may cause thermomechanical stresses [8]. In
thermistors the resistivity (and therefore also the
strength of the heat source) strongly depends on the
temperature. In these materials thermal gradients (which
occur in any component) cause a strongly inhomogene-
ous distribution of heat sources which again influence
the temperature and the electric field. This highly non-
linear problem of mutual interactions has to be solved in
order to determine the temperature field and the ther-
momechanical stress and strain field.
Over a long time scale, the load spectrum might
change due to degrading electrical properties
[9,10].
These not fully understood kind of aging processes lead
to a change of the heat source distribution and conse-
quently also influence the thermo-mechanical loads.
These additional changes in strains and stresses
must also be accounted for, but up to now, only rela-
tively little theoretical work on these problems were
performed. In the present work a short summary on state
of the art of the mechanical loading and failure of high
power varistors and PTC-devices will be given.
Reliability analysis
In ceramics failure generally originates at flaws,
which are sparsely distributed inhomogeneities in the
material and which can, in general, be described like
cracks
[I
1, 121. Fracture starts if
-
at the location of the
"crack"
-
the stress intensity factor exceeds the fracture
toughness (this criterion is called the Griffith criterion).
The failure stress (the strength) depends on the size and
orientation
of
the flaws and on the fracture toughness
of
the material [13]. For
a
given material the strength is
high if the most critical flaw is short and vice Vera. In
general the size of flaws is not exactly
known
and differs
from component to component. Therefore the strength
325