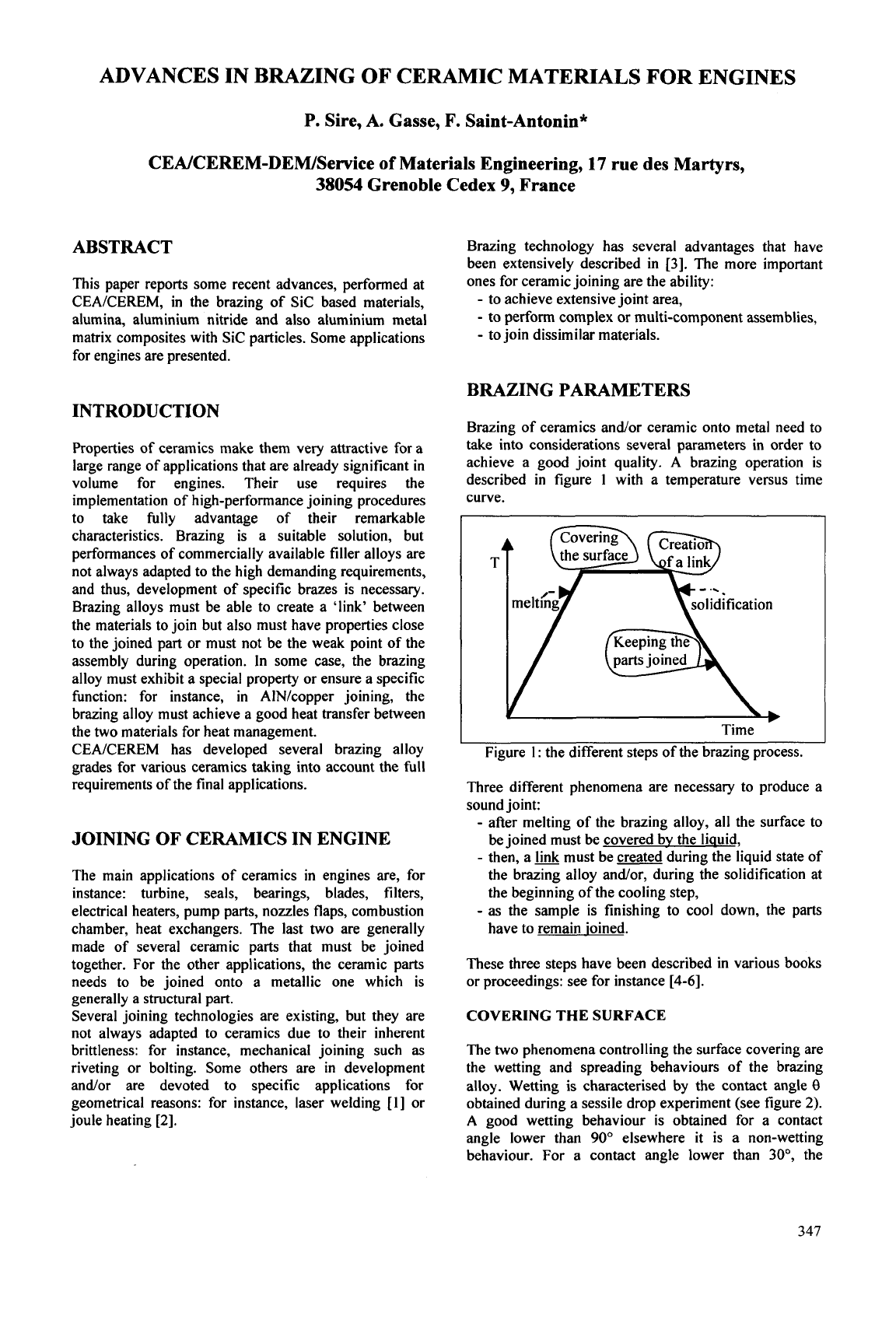
ADVANCES IN BRAZING
OF
CERAMIC MATERIALS
FOR
ENGINES
P. Sire, A. Gasse, F. Saint-Antonin*
CENCEREM-DEWService
of
Materials Engineering,
17
rue des Martyrs,
38054
Grenoble Cedex
9,
France
ABSTRACT
This paper reports some recent advances, performed at
CEAKEREM,
in
the brazing of Sic based materials,
alumina, aluminium nitride and also aluminium metal
matrix composites with Sic particles. Some applications
for engines are presented.
Brazing technology has several advantages that have
been extensively described in
[3].
The more important
ones for ceramic joining are the ability:
-
to achieve extensive joint area,
-
to perform complex
or
multi-component assemblies,
-
to join dissimilar materials.
BRAZING PARAMETERS
INTRODUCTION
Properties
of
ceramics make them very attractive for a
large range of applications that are already significant
in
volume for engines. Their use requires the
implementation of high-performance joining procedures
to take hlly advantage of their remarkable
characteristics. Brazing is a suitable solution, but
performances
of
commercially available filler alloys are
not always adapted to the high demanding requirements,
and thus, development of specific brazes
is
necessary.
Brazing alloys must be able to create a 'link' between
the materials to join but also must have properties close
to the joined part or must not be the weak point of the
assembly during operation. In some case, the brazing
alloy must exhibit a special property
or
ensure a specific
function: for instance, in AINkopper joining, the
brazing alloy must achieve a good heat transfer between
the two materials for heat management.
CEAKEREM has developed several brazing alloy
grades for various ceramics taking into account the full
requirements of the final applications.
JOINING OF CERAMICS IN ENGINE
The main applications of ceramics in engines are, for
instance: turbine, seals, bearings, blades, filters,
electrical heaters, pump parts, nozzles flaps, combustion
chamber, heat exchangers. The last two are generally
made of several ceramic parts that must be joined
together. For the other applications, the ceramic parts
needs to be joined onto a metallic one which is
generally a structural part.
Several joining technologies are existing, but they are
not always adapted to ceramics due to their inherent
brittleness: for instance, mechanical joining such
as
riveting
or
bolting. Some others are in development
and/or are devoted to specific applications for
geometrical reasons: for instance, laser welding
[l]
or
joule heating
[2].
Brazing
of
ceramics and/or ceramic onto metal need to
take into considerations several parameters in order to
achieve a good joint quality.
A
brazing operation is
described
in
figure
1
with a temperature versus time
curve.
T
Time
Figure
1
:
the different steps of the brazing process.
Three different phenomena are necessary to produce a
sound joint:
-
after melting of the brazing alloy, all the surface to
be joined must be covered bv the liauid,
-
then, a must be created during the liquid state of
the brazing alloy andor, during the solidification at
the beginning of the cooling step,
-
as
the sample is finishing to cool down, the parts
have to remain ioined.
These three steps have been described in various books
or proceedings: see for instance
[4-61.
COVERING THE SURFACE
The two phenomena controlling the surface covering are
the wetting and spreading behaviours of the brazing
alloy. Wetting is characterised by the contact angle
8
obtained during a sessile drop experiment (see figure
2).
A
good wetting behaviour is obtained for a contact
angle lower than
90"
elsewhere it is a non-wetting
behaviour.
For a contact angle lower than
30°,
the
347