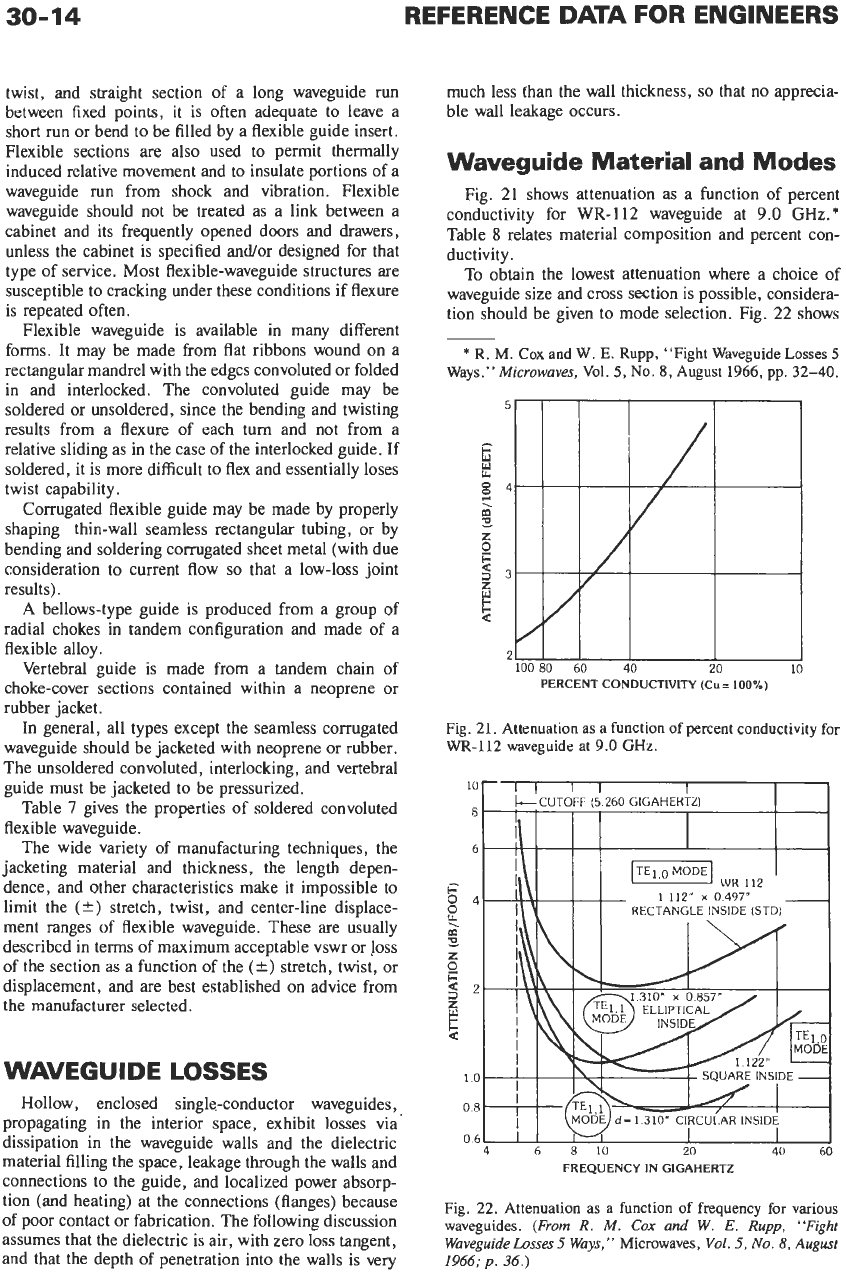
30-14
REFERENCE
DATA
FOR ENGINEERS
twist, and straight section of a long waveguide run
between fixed points, it is often adequate to leave a
short run or bend to be filled by a flexible guide insert.
Flexible sections
are
also used to permit thermally
induced relative movement and to insulate portions
of
a
waveguide run from shock and vibration. Flexible
waveguide should not be treated as a link between a
cabinet and its frequently opened doors and drawers,
unless the cabinet is specified and/or designed for that
type
of
service. Most flexible-waveguide structures are
susceptible
to
cracking under these conditions if flexure
is
repeated often.
Flexible waveguide is available in many different
forms. It may be made from flat ribbons wound on a
rectangular mandrel with the edges convoluted or folded
in and interlocked. The convoluted guide may be
soldered or unsoldered, since the bending and twisting
results from a flexure of each turn and not from a
relative sliding as in the case of the interlocked guide. If
soldered, it is more difficult to flex and essentially loses
twist capability.
Corrugated flexible guide may be made by properly
shaping thin-wall seamless rectangular tubing, or by
bending and soldering corrugated sheet metal (with due
consideration to current flow
so
that a low-loss joint
results).
A
bellows-type guide is produced from a group of
radial chokes in tandem configuration and made of a
flexible alloy.
Vertebral guide is made from a tandem chain of
choke-cover sections contained within a neoprene or
rubber jacket.
In
general, all types except the seamless corrugated
waveguide should be jacketed with neoprene or rubber.
The unsoldered convoluted, interlocking, and vertebral
guide must be jacketed to be pressurized.
Table
7
gives the properties of soldered convoluted
flexible waveguide.
The wide variety of manufacturing techniques, the
jacketing material and thickness, the length depen-
dence, and other characteristics make it impossible to
limit the
(e)
stretch, twist, and center-line displace-
ment ranges of flexible waveguide. These are usually
described in terms of maximum acceptable vswr or
loss
of the section as a function of the
(C)
stretch, twist, or
displacement, and are best established on advice from
the manufacturer selected.
WAVEGUIDE
LOSSES
Hollow, enclosed single-conductor waveguides,
propagating in the interior space, exhibit losses via
dissipation in the waveguide walls and the dielectric
material filling the space, leakage through the walls and
connections to the guide, and localized power absorp-
tion (and heating) at the connections (flanges) because
of poor contact or fabrication. The following discussion
assumes that the dielectric is air, with zero loss tangent,
and that the depth of penetration into the walls is very
much less than the wall thickness,
so
that no apprecia-
ble wall leakage occurs.
Waveguide Material and Modes
Fig.
21
shows attenuation as a function of percent
conductivity for
WR-112
waveguide at
9.0
GHz.*
Table
8
relates material composition and percent con-
ductivity.
To obtain the lowest attenuation where a choice of
waveguide size and cross section is possible, considera-
tion should be given to mode selection. Fig.
22
shows
*
R.
M.
Cox
and
W.
E.
Rupp,
“Fight Waveguide
Losses
5
Ways.”
Microwaves,
Vol.
5,
No.
8,
August 1966,
pp.
32-40.
~~
PERCENT CONDUCTIVITY (Cu
=
100%)
Fig.
21.
Attenuation
as
a
function
of
percent conductivity
for
WR-112 waveguide
at
9.0
GHz.
FREQUENCY IN GIGAHERTZ
Fig. 22.
Attenuation
as
a
function
of
frequency
for
various
waveguides.
(From
R.
M.
Cox
and
W.
E.
Rupp,
“Fight
Waveguidehsses
5
Ways,”
Microwaves,
Vol.
5,
No.
8,
August
1966;
p.
36.)