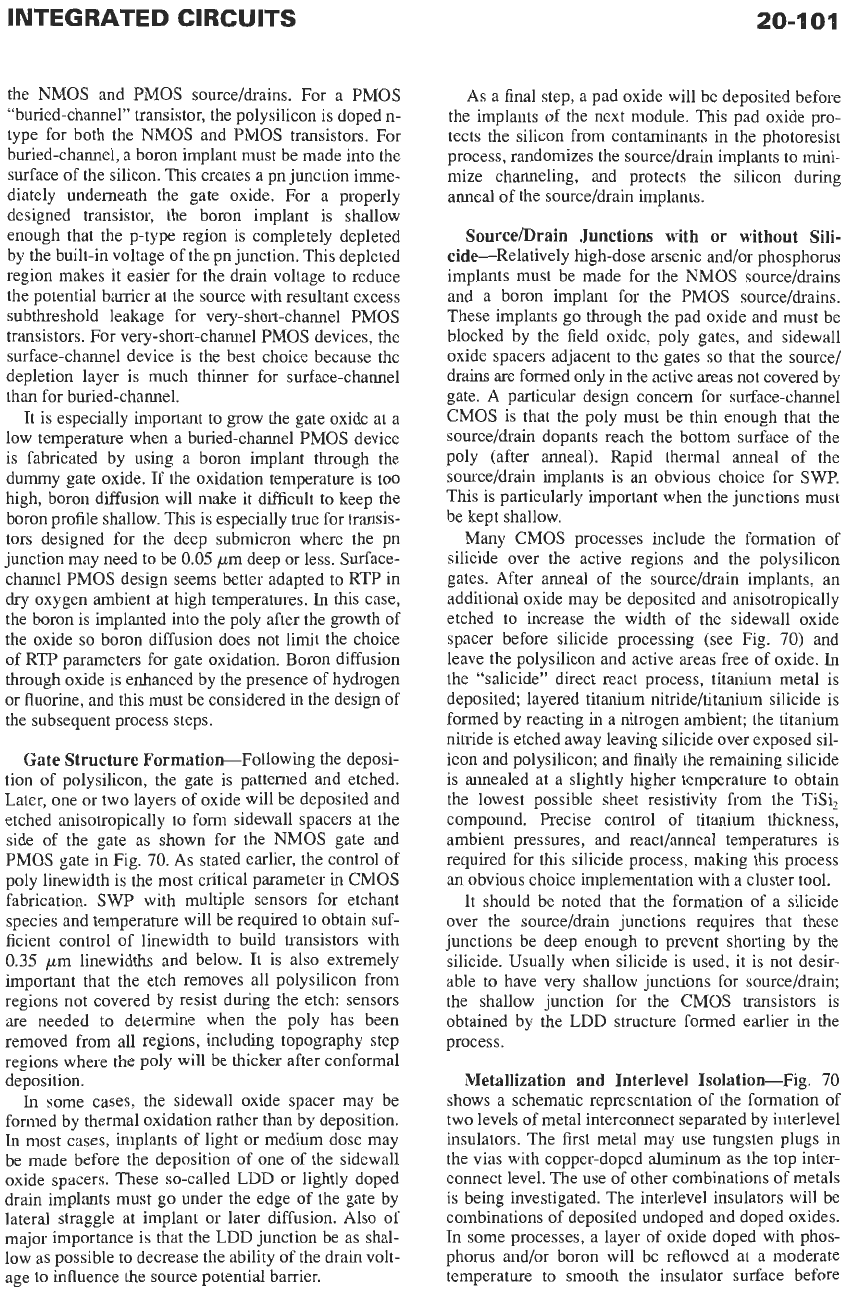
20-1
01
the NMOS and PMOS source/drains. For a PMOS
“buried-channel” transistor, the polysilicon is doped
n-
type for both the
NMOS
and PMOS transistors. For
buried-channel, a boron implant must be made into the
surface of the silicon. This creates a pn junction imme-
diately underneath the gate oxide. For a properly
designed transistor, the boron implant is shallow
enough that the p-type region is completely depleted
by the built-in voltage of the pn junction. This depleted
region makes it easier for the drain voltage to reduce
the potential barrier at the source with resultant excess
subthreshold leakage for very-short-channel PMOS
transistors. For very-short-channel PMOS devices, the
surface-channel device is the best choice because the
depletion layer
is
much thinner for surface-channel
than for buried-channel.
It is especially important to grow the gate oxide at a
low temperature when a buried-channel PMOS device
is fabricated by using a boron implant through the
dummy gate oxide. If the oxidation temperature is too
high, boron diffusion will make it difficult to keep the
boron profile shallow. This is especially true for transis-
tors designed for the deep submicron where the pn
junction may need
to
be
0.05
pm deep or less. Surface-
channel PMOS design seems better adapted to RTP in
dry
oxygen ambient at high temperatures.
In
this case,
the boron is implanted into the poly after the growth of
the oxide
so
boron diffusion does
not
limit the choice
of
RTP
parameters for gate oxidation. Boron diffusion
through oxide
is
enhanced by the presence of hydrogen
or fluorine, and this must be considered in the design of
the subsequent process steps.
Gate Structure Formation-Following the deposi-
tion of polysilicon, the gate is patterned and etched.
Later, one or two layers of oxide will be deposited and
etched anisotropically to form sidewall spacers at the
side of the gate as shown for the
NMOS
gate and
PMOS
gate in Fig.
70.
As stated earlier, the control of
poly linewidth is the most critical parameter in CMOS
fabrication.
SWP
with multiple sensors for etchant
species and temperature will be required
to
obtain suf-
ficient control of linewidth to build transistors with
0.35
pm linewidths and below. It is also extremely
important that the etch removes all polysilicon from
regions not covered by resist during the etch: sensors
are needed to determine when the poly has been
removed from all regions, including topography step
regions where the poly will be thicker after conformal
deposition.
In
some cases, the sidewall oxide spacer may be
formed by thermal oxidation rather than by deposition.
In
most cases, implants of light or medium dose may
be made before the deposition
of
one of the sidewall
oxide spacers. These so-called LDD or lightly doped
drain implants must go under the edge
of
the gate by
lateral straggle at implant or later diffusion. Also of
major importance is that the LDD junction be as shal-
low as possible to decrease the ability of the drain volt-
age
to
influence the source potential barrier.
As a final step, a pad oxide will be deposited before
the implants of the next module. This pad oxide pro-
tects the silicon from contaminants in the photoresist
process, randomizes the source/drain implants to mini-
mize channeling, and protects the silicon during
anneal of the source/drain implants.
Source/Drain Junctions with or without Sili-
cide-Relatively high-dose arsenic and/or phosphorus
implants must be made for the
NMOS
source/drains
and a boron implant for the PMOS source/drains.
These implants go through the pad oxide and must be
blocked by the field oxide, poly gates, and sidewall
oxide spacers adjacent to the gates
so
that the source/
drains
are formed
only
in the active areas not covered by
gate. A particular design concern for surface-channel
CMOS is that the poly must be thin enough that the
source/drain dopants reach the bottom surface of the
poly (after anneal).
Rapid thermal anneal of the
source/drain implants is an obvious choice for
SWP.
This is particularly important when the junctions must
be kept shallow.
Many CMOS processes include the formation of
silicide over the active regions and the polysilicon
gates. After anneal of the source/drain implants, an
additional oxide may be deposited and anisotropically
etched to increase the width of the
sidewall oxide
spacer before silicide processing (see Fig.
70)
and
leave the polysilicon and active areas free of oxide.
In
the “salicide” direct react process, titanium metal is
deposited; layered titanium nitride/titanium silicide is
formed by reacting in a nitrogen ambient; the titanium
nitride is etched away leaving silicide over exposed sil-
icon and polysilicon; and finally the remaining silicide
is
annealed at a slightly higher temperature to obtain
the lowest possible sheet resistivity from the TiSi,
compound. Precise control of titanium thickness,
ambient pressures, and react/anneal temperatures is
required for this silicide process, making this process
an obvious choice implementation with a cluster tool.
It
should be noted that the formation of a silicide
over the source/drain junctions requires that these
junctions be deep enough to prevent shorting by the
silicide. Usually when silicide is used,
it
is not desir-
able to have very shallow junctions for source/drain;
the shallow junction for the CMOS transistors is
obtained by the
LDD
structure formed earlier in the
process.
Metallization and Interlevel Isolation-Fig.
70
shows a schematic representation
of
the formation of
two levels of metal interconnect separated by interlevel
insulators. The first metal may use tungsten plugs in
the vias with copper-doped aluminum as the top inter-
connect level. The use of other combinations of metals
is being investigated. The interlevel insulators will be
combinations of deposited undoped and doped oxides.
In some processes, a layer of oxide doped with phos-
phorus and/or boron will be reflowed at a moderate
temperature to smooth the insulator surface before