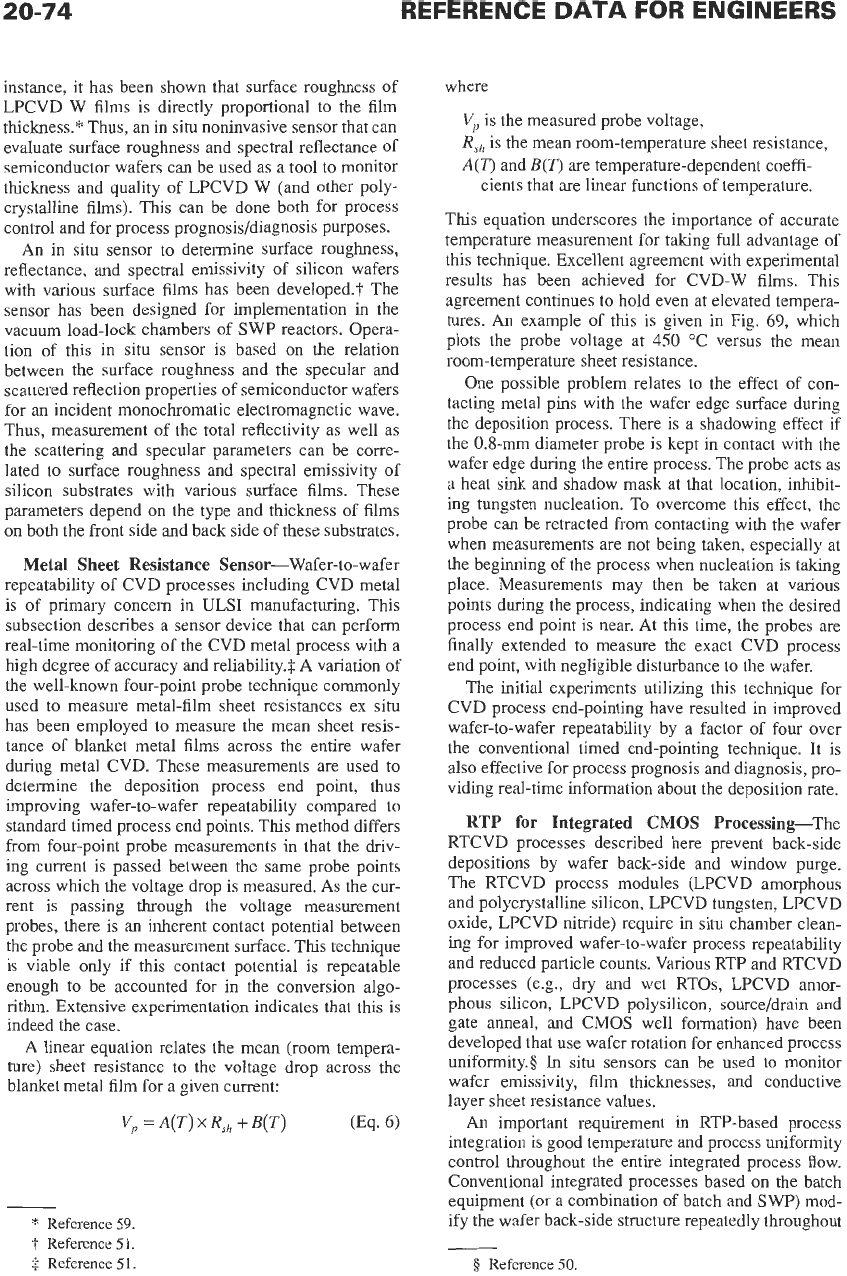
20-74
instance, it has been shown that surface roughness of
LPCVD W films is directly proportional to the film
thickness.* Thus, an in situ noninvasive sensor that can
evaluate surface roughness and spectral reflectance of
semiconductor wafers can be used as a tool
to
monitor
thickness and quality of LPCVD W (and other poly-
crystalline films). This can be done both for process
control and for process prognosis/diagnosis purposes.
An in situ sensor to determine surface roughness,
reflectance, and spectral emissivity of silicon wafers
with various surface films has been developed.? The
sensor has been designed for implementation in the
vacuum load-lock chambers of SWP reactors. Opera-
tion of this in situ sensor is based on the relation
between the surface roughness and the specular and
scattered reflection properties of semiconductor wafers
for an incident monochromatic electromagnetic wave.
Thus, measurement of the total reflectivity as well as
the scattering and specular parameters can be corre-
lated to surface roughness and spectral emissivity of
silicon substrates with various surface films. These
parameters depend on the type and thickness of films
on both the front side and back side of these substrates.
Metal Sheet Resistance Sensor-Wafer-to-wafer
repeatability of CVD processes including CVD metal
is of primary concern in ULSI manufacturing. This
subsection describes a sensor device that can perform
real-time monitoring
of
the CVD metal process with a
high degree of accuracy and reliability.$. A variation of
the well-known four-point probe technique commonly
used to measure metal-film sheet resistances ex situ
has been employed to measure the mean sheet resis-
tance of blanket metal films across the entire wafer
during metal CVD. These measurements are used to
determine the deposition process end point, thus
improving wafer-to-wafer repeatability compared
to
standard timed process end points. This method differs
from four-point probe measurements in that the driv-
ing current is passed between the same probe points
across which the voltage drop is measured. As the cur-
rent is passing through the voltage measurement
probes, there is an inherent contact potential between
the probe and the measurement surface. This technique
is viable only if this contact potential is repeatable
enough to be accounted for in the conversion algo-
rithm. Extensive experimentation indicates that this is
indeed the case.
A linear equation relates the mean (room tempera-
ture) sheet resistance
to
the voltage drop across the
blanket metal film for a given current:
V,
=
A(T)
x
R,,
+
B(T)
*
Reference
59.
t
Reference
5
1.
i
Reference
5
1.
where
Vp
is the measured probe voltage,
R,,
is the mean room-temperature sheet resistance,
A(T)
and
B(T)
are temperature-dependent coeffi-
cients that are linear functions of temperature.
This equation underscores the importance of accurate
temperature measurement for taking full advantage of
this technique. Excellent agreement with experimental
results has been achieved for CVD-W films. This
agreement continues to hold even at elevated tempera-
tures.
An
example of
this
is given in Fig.
69,
which
plots the probe voltage at
450
"C versus the mean
room-temperature sheet resistance.
One possible problem relates
to
the effect of con-
tacting metal pins with the wafer edge surface during
the deposition process. There is a shadowing effect if
the 0.8-mm diameter probe is kept in contact with the
wafer edge during the entire process. The probe acts as
a heat
sink
and shadow mask at that location, inhibit-
ing tungsten nucleation. To overcome this effect, the
probe can be retracted from contacting with the wafer
when measurements are not being taken, especially at
the beginning of the process when nucleation is taking
place. Measurements may then be taken at various
points during the process, indicating when the desired
process end point is near. At this time, the probes are
finally extended to measure the exact CVD process
end point, with negligible disturbance to the wafer.
The initial experiments utilizing this technique for
CVD process end-pointing have resulted
in
improved
wafer-to-wafer repeatability by a factor of four over
the conventional timed end-pointing technique. It is
also
effective for process prognosis and diagnosis, pro-
viding real-time information about the deposition rate.
RTP for Integrated
CMOS
Processing-The
RTCVD processes described here prevent back-side
depositions by wafer back-side and window purge.
The RTCVD process modules (LPCVD amorphous
and polycrystalline silicon, LPCVD tungsten, LPCVD
oxide, LPCVD nitride) require in situ chamber clean-
ing for improved wafer-to-wafer process repeatability
and reduced particle counts. Various RTP and RTCVD
processes (e.g., dry and wet RTOs, LPCVD amor-
phous silicon, LPCVD polysilicou, sourcetdrain
and
gate anneal, and CMOS well formation) have been
developed that use wafer rotation for enhanced process
uniformity.§
In
situ sensors can be used to monitor
wafer emissivity, film thicknesses, and conductive
layer sheet resistance values.
An
important requirement in RTP-based process
integration is good temperature and process uniformity
control throughout the entire integrated process flow.
Conventional integrated processes based
on
the batch
equipment (or a combination of batch and
SWP)
mod-
ify the wafer back-side structure repeatedly throughout
5
Reference
50.