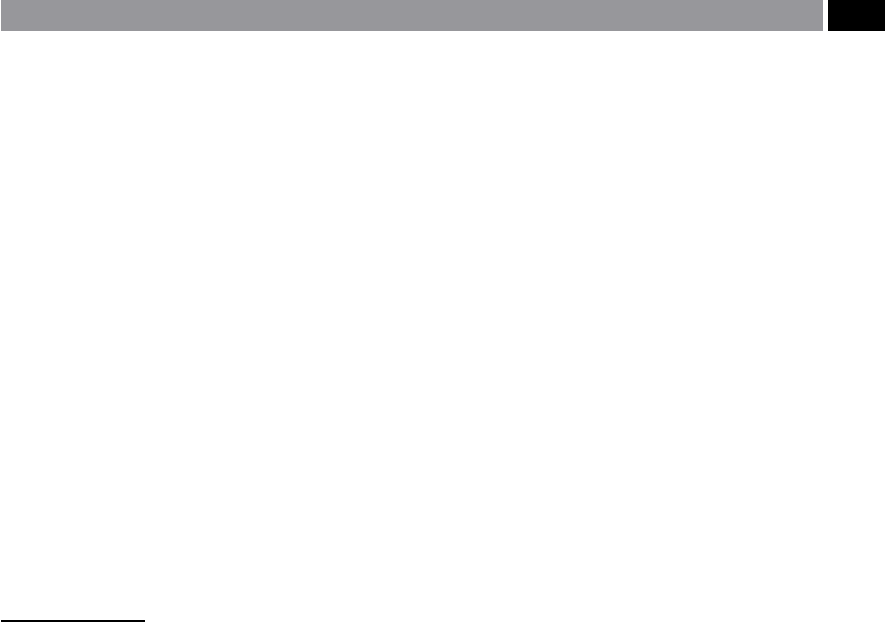
not possible to index the turning centre’s turret, due
to the nature of the electrical couplings to the plat-
form, but this problem can be overcome by mounting
a dierent dynamometer conguration, situating the
sensing equipment within the turret – as depicted in
Fig. 179a. Here, the installation of an acoustic emission
sensor (AE)
76
behind the turret in combination with
a multi-component force sensor mounted in the tur-
ret’s pocket – this force equipment having previously
required the necessary of preloading which was pro-
vided by a suitable ‘preload wedge’.
In Fig. 179b, are exhibited the measuring results
from the sensor installation decribed in Fig. 179a – for
a longitudinal (external) turning operation, with the
cutting force components and the AE signals being
simultaneously recorded. e resulting graphs pro-
duced in both Figs. 179bi and bii, show the AE rms
77
and force signals in the case of a tool breakage. e
tool breakage can be readily seen in both signal traces.
Figs. 179biii and biv, show the AE and force sensor sig-
76 Acoustic emission sensors (AE), in metal machining applica-
tions usually capture frequencies in the range of 50 kHz to
>1 MHz in range, this being a usual aid for any form of in-
process monitoring operations. By using a combination of AE
and force monitoring, this has been shown to be a means of
condition monitoring of the cutting tool’s state – more will
be said on this topic later. In metal cutting operations AE oc-
curs due to plasto-mechanical processes of crack formation
and chip removal, in combination with surface friction. Any
form of tool wear alters the contact surfaces between the tool
and workpiece, inuencing and increasing the AE signal in-
tensity. Hence, advanced warning of potential tool breakage
sometimes results in the appearance of micro-ssures in the
tool, which cause an escalation of the AE signals – allowing
a basic form of tool and process monitoring to be achieved.
AE generation in metallic machining operations, can extend
over frequencies of several MHz, although the signal intensity
is normally very low and diminishes with increasing distance
from its source. Any form of machine vibrations and inter-
ferences from the local environment introduce signals from
a low frequency range, meaning that any form of signicant
analysis is normally only possible above 50 kHz. Machine tool
interference sources are usually the result of either electrical,
or hydraulic main and feed drives, as well as from bearing
noise, spindles and gears. ese unwanted interferences can
be suppressed by utilising suitable high-pass lters, or alterna-
tively a well-designed AE sensor(s), with inherent high-pass
frequency characteristics.
77 ‘Root mean square’ (rms), is a measure of the eective mean
current of an alternating current. Its actual rms value is de-
rived from the power dissipation by an ac current.
nals respectively, on the ‘over-turning’ of transversal
holes present in the external turning of the workpiece.
Hence, the interrupted cut can clearly be seen peri-
odically in the resultant force traces. In Fig. 179biii,
the AE rms signal shows this interference, albeit not
very well pronounced, unlike that of the force trace
produced in Fig. 179biv, where a denite noise spike
can be seen. is combination of two complementary
sensing elements and their sensor signals, allows the
reliable detection of a process fault, such as tool break-
age detection.
Until approximately the mid-1990’s, commercial
versions of cutting force monitoring equipment for the
measurement of a rotating cutting tool, or an edge was
not readily available for: drilling, reaming, tapping
and milling applications. A major advantage of these
rotating cutting force dynamometers, is that they can
be used for multi-axes contour milling applications,
or simply for an investigation of a discrete tool’s cut-
ting edge geometry and its anticipated machining per-
formance. An early version of such a rotating cutting
force dynamometer, is depicted in Fig. 180a.
In Fig. 180b, graphs have been produced showing
the cutting force and torque results respectively, pro-
duced by the rotating cutting force dynamometer. In-
terest frequently centres on the forces and moments
acting on the rotating tool. A rotating cutting force
dynamometer (Fig. 180a), allows measurement of
three orthogonal forces: ‘F
X
’ , ‘F
Y
’ , ‘F
Z
’ , together with
the moment ‘M
Z
’. e data measured by the rotating
dynamometer occurs via miniature charge ampliers,
which are then transferred by telemetry to an appro-
priately positioned stationary antenna. e telemetry
involves a bi-directional transmission, with measured
data being transmitted to the ‘stationary side’ of the
monitoring system and any control commands for the
integral charge ampliers transmitted to the appropri-
ate section of the rotating dynamometer. e power
supply to the electronics in the rotor, occurs by the
same antenna, but having a dierent carrier frequency
to that of the data transfer. Typical resultant signals
produced by the rotating dynamometer are shown in
Fig. 180b and have been ‘zoomed’ for the investigation
of a single drill’s cutting edge.
Cutting force dynamometers of various congu-
rations, are invaluable tools for any form of in-depth
machinability study, as they indicate the precise condi-
tions at the cutting tool’s edge(s), in a truly dynamic
situation. All dynamometers that are purchased from
the manufacturer must come with an appropriate cali-
Machinability and Surface Integrity 347