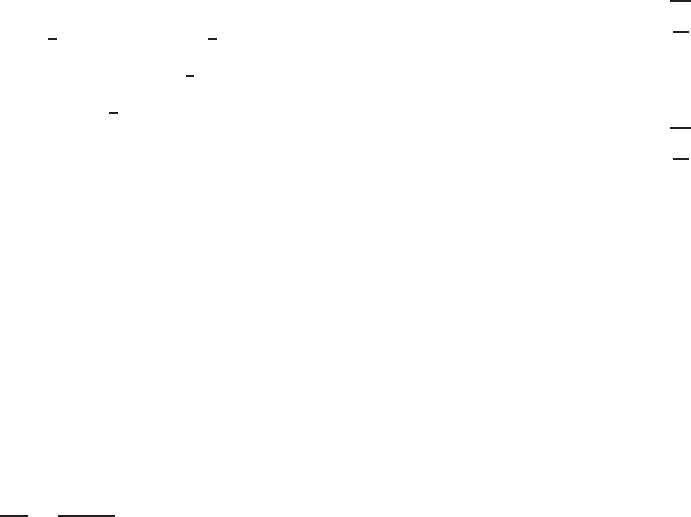
120 4 FLEXURAL MEMBERS
Since y
c
/t < λ
l
, OK. Therefore, the nominal
moment is determined as
M
n
= F
y
t[b
c
y
c
+
4
3
(y
p
)
2
+ 2y
tp
(y
p
+
1
2
y
tp
) + b
t
y
t
]
= 50(0.135)[(3.754 × 3.46) +
4
3
(3.46)
2
+ 2(0.945)(3.46 +
1
2
× 0.945)
+ 1.865(4.405)]
= 301.05 in. -kips
5. Yield Moment. Based on the method illustrated in
Example 4.1, the effective yield moment M
y
is
M
y
= 248.0in.-kips
1.25M
y
= 310.0in.-kips
6. Nominal Moment and Allowable Moment. Because M
n
is less than 1.25M
y
,useM
n
for the nominal moment,
that is,
M
n
= 301.05 in.-kips
The allowable design moment is
M
a
=
M
n
b
=
301.05
1.67
= 180.27 in.-kips
B. LRFD Method.
The nominal moment for the LRFD method is the same as
that computed for the ASD method. From item A above,
the nominal moment about the x axis of the I-section with
unequal flanges is
M
n
= 301.05 in.-kips
Based on Section 4.2.1 or Section C3.1.1 of the North
American Specification, the design moment for the
I-section having an unstiffened compression flange (φ
b
= 0.90) is
φ
b
M
n
= 0.90(301.05) = 270.95 in.-kips
4.2.2.4 Economic Design for Bending Strength The
above discussion and design examples are based on the fact
that the allowable design moment is determined for a given
section for which the dimensions are known. In the design
of a new section, the dimensions are usually unknown
factors. The selection of the most favorable dimensions can
be achieved by using the optimum design technique. This
is a very complex nonlinear problem which can only be
solved by computer analysis.
1.247
However, if the depth and
the thickness of the section are known, previous study has
shown that the maximum moment-to-weight ratio usually
occurs in the neighborhood of the flange width determined
by Eq. (4.21) or (4.22) as applicable:
1. For unstiffened compression flanges,
w = 0.43t
E
f
(4.21)
2. For stiffened c ompression flanges supported by a web
on each longitudinal edge,
w = 1.28t
E
f
(4.22)
where w = flat width for compression flange
t = thickness of steel
E = modulus of elasticity
f = maximum compressive edge stress in the
element without considering the safety
factor
The economic design of continuous beams and long-span
purlins is discussed in Refs. 4.11 and 4.12.
4.2.2.5 Deflection of Flexural Members For a given
loading condition, the deflection of flexural members
depends on the magnitude, location, and type of the
applied load, the span length, and the bending stiffness EI ,
in which the modulus of elasticity in the elastic range is
29.5 × 10
3
ksi (203 GPa or 2.07×10
6
kg/cm
2
)andI is the
moment of inertia of the beam section.
Similar to the bending strength calculation, the determi-
nation of the moment of inertia I for calculating the deflec-
tion of steel beams is based on the effective areas of the
compression flange, edge stiffer, and beam web, for which
the effective widths are computed for the compressive stress
developed from the bending moment. If the compression
flange, edge stiffer, and beam web are fully effective, the
moment of inertia is obviously based on the full section. In
this case, the moment of inertia is a constant value along
the entire beam length. Otherwise, if the moment of inertia
is on the basis of the effective areas of the compression
flange, edge stiffener, and/or beam web, the moment of
inertia may vary a long the beam span because the bending
moment usually varies along the beam length, as shown in
Fig. 4.22.
In the design of thin-walled cold-formed steel sections,
the method to be used for deflection calculation is based on
the accuracy desired in the analysis. If a more exact deflec-
tion is required, a computer program or a numerical method
may be used in which the beam should be divided into a
relatively large number of elements according to variable
moments of inertia. The deflection calculation for such a
beam is too complicated for hand calculation. On the other
hand, if an approximate analysis is used, the deflection of
a simply supported beam may be computed on the basis of