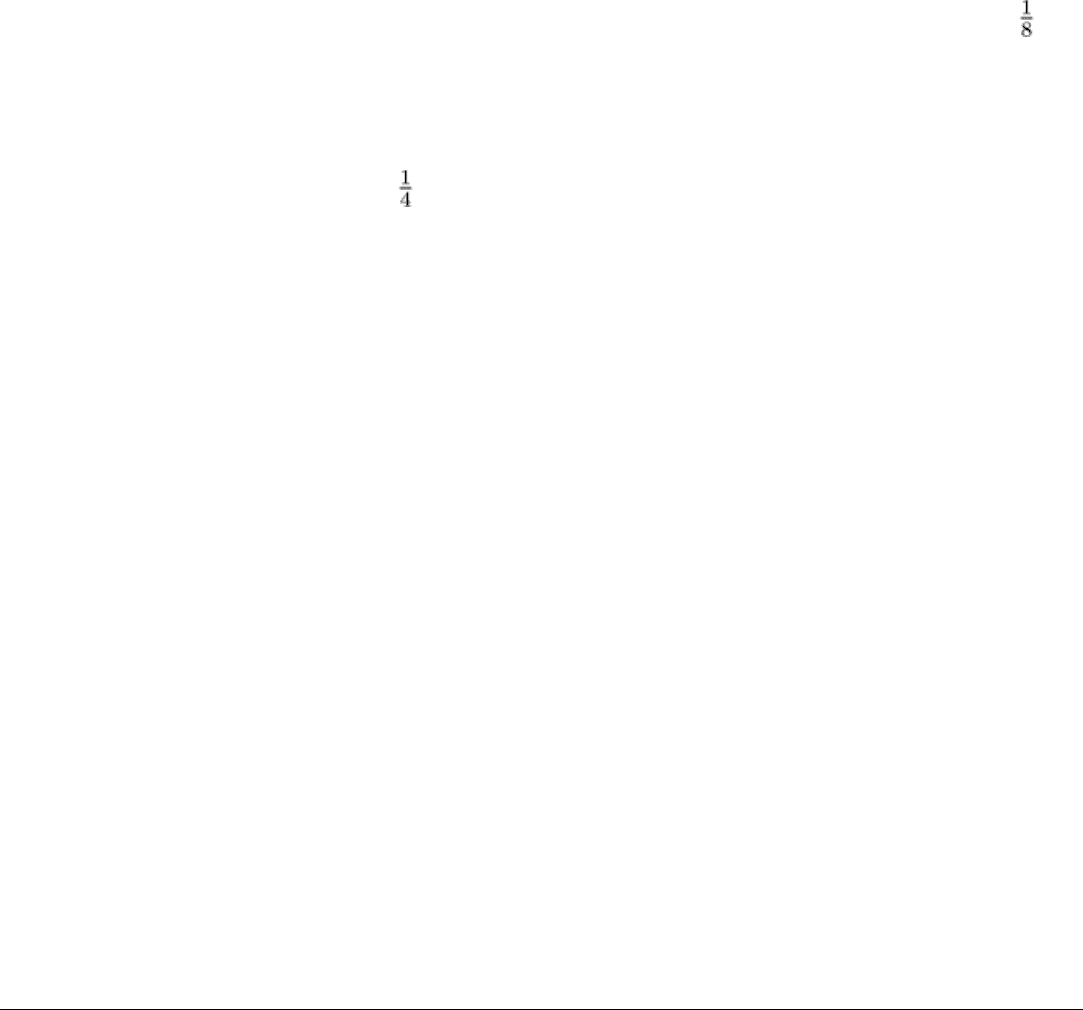
Nitriding minimizes or prevents galling of dies made of alloy steels or alloy tool steels (such as A2 or D2) that contain
chromium and molybdenum. However, the nitrided surfaces may spall off at radii smaller than about 3.2 mm ( in.),
especially from dies having very complex contours.
Hard chromium plating usually eliminates galling of mild steel, alloy steel, and tool steel dies, and it is often used for
severe duty. For operations involving high local pressures, hardened alloy steels or tool steels are less likely to yield
plastically and cause cracking of the hard chromium plating. With dies for complex parts, hard chromium plating may
spall off at radii smaller than about 6.4 mm ( in.).
For some press forming operations, dies made from tool steels other than those discussed above may be desirable. For
example, shock-resistant tool steels such as S1, S5, and S7 may be used for die components subjected to severe impact in
service. H11 and H13, possibly nitrided for greater wear resistance, also may be used for such components. In press
forming operations requiring significantly greater wear life than is routinely attained with D2 or nitrided D2, it may be
necessary to specify a more wear-resistant cold work tool steel such as A7, D3, D4, or D7, or a high-speed steel such as
M2, M4, or T15. Cost generally determines the desirability of changing to an alternative material, although toughness
may also be a determining factor. Costs to be considered include not only material costs but also tool fabrication costs and
the cost of periodic resharpening.
Other Tool Materials. Significant advances have been made in recent years in the area of tool steels made by powder
metallurgy (P/M) techniques. For example, P/M high-speed steels, hot isostatically pressed to full density, offer greater
ease of fabrication and significantly improved toughness compared to conventional ingot-cast steels of the same
compositions. New grades that could not have been produced economically by conventional steelmaking practices have
been introduced through the use of powder metallurgy. One such alloy is Crucible CPM 10V (Fe-2.45C-5.0Cr-9.75V-
1.25Mo), which is an air-hardened cold-work tool steel designed specifically for tooling applications requiring long wear
life and good toughness. This material can be a cost-effective alternative to carbide in applications in which breaking or
chipping of carbide is a problem or in which the full potential of carbide is either not realized or not required. More
information on these materials is available in the article "Particle Metallurgy Tool Steels" in Powder Technologies and
Applications, Volume 7 of the ASM Handbook.
When maximum resistance to galling and wear is required, cemented carbides have traditionally been recognized as the
ultimate tooling materials. However, because of the high cost of these materials and their tendency to be brittle in service,
carbides are frequently used only for inserts in critical die areas. These inserts are usually made of a straight grade of
tungsten carbide containing about 6% cobalt binder, but higher cobalt contents can be specified to provide greater shock
resistance. The more recently developed steel-bonded carbides offer greater ease of fabrication and very often can be
demonstrated to be cost-effective substitutes for the more costly cemented carbides with cobalt binder.
These materials use tool steel or stainless steel matrices filled with titanium carbide at volume fractions ranging from 15
to 45%. Several grades are available.
Selection of Material for Deep-Drawing Dies
Introduction
DEEP DRAWING is a process in which sheet metal is formed into round or square cup-shaped parts by making it
conform to a punch as it is drawn through a die (see the article "Deep Drawing" in this Volume). In conventional deep
drawing, successive draws are made in the same direction. The types of dies and other tooling used for conventional deep
drawing are illustrated in Fig. 1.