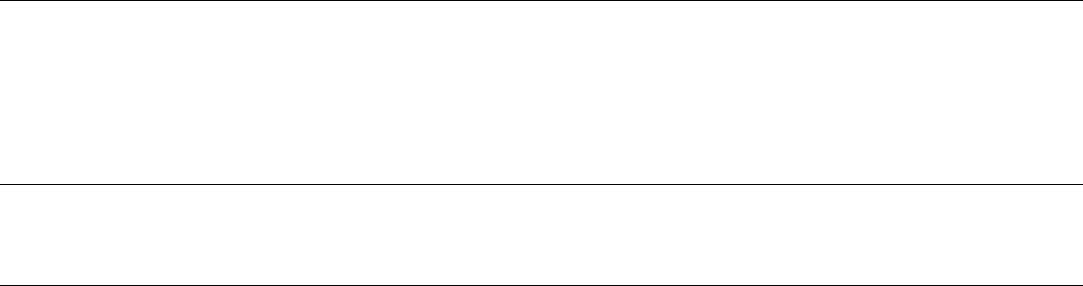
including silicones, amides, glycols, and fine particles of selected solids such as silica. The concentration of these agents
needed for effective foam control is low; however, monitoring concentration to maintain control may be a problem.
Solid lubricants are often suspended in oil- or water-base fluids for extremely heavy-duty forming of sheet metal.
These solids are graphite, carbonates, mica, Teflon, nylon, metal powders, and molybdenum disulfide. Buildup on tooling
and cleaning of workpieces are potential problems during operations with these suspended-solid lubricants.
Corrosion inhibitors are frequently added to both water- and oil-base lubricants to provide part protection during
processing and storage. Part corrosion may be a particularly difficult problem when water-base lubricants are used;
however, sulfonates, carboxylates, borates, and phosphonates have been successful in alleviating corrosion. In oil-base
lubricants, organic amines and sulfonates, as well as phosphates and unsaturated fatty acids, have been used successfully.
Toluyltriazole has been used successfully to protect copper sheet from staining and corrosion.
Antimicrobial agents may be required in order to prevent the growth of anaerobic or aerobic bacteria. Bacteria
frequently cause various operating problems (corrosion, odor, buildup of lubricant on workpieces, or emulsion instability)
in emulsions or solutions that contain oil and water. In solutions formulated with various chemical components, bacteria
will generally not be the problem; rather, formation of mold can cause malfunction of pumps and filters, and buildup on
tooling and workpiece surfaces. It may also alter the solution chemistry. Biocides are not required when lubricant
application does not involve repeated use or recirculation of the fluid. Care in handling as well as monitoring are
important if biocides are to be used safely and effectively.
References cited in this section
4.
E. Nachtman and S. Kalpakjian, Lubricants and Lubrication in Metalworking Operations,
1985, p 63-105
5.
J. Schey, Tribology in Metalworking, American Society for Metals, 1983, p 131-175
Selection and Use of Lubricants in Forming of Sheet Metal
Elliot S. Nachtman, Tower Oil & Technology Company
Lubricant Effectiveness
Selection of an appropriate lubricant for a specific sheet metal forming operation or for a series of different operations is
often a costly hit-or-miss proposition. There are, however, laboratory test procedures that can often reduce the possibility
of error.
Because of the difficulty of translating laboratory test results to an operating condition, several simulation tests have been
developed to screen lubricants for sheet metal forming. Small-capacity presses have been installed as test machines with
the ability to control speed of forming, metallurgy of tools and work metal, and lubricant application method.
Strip drawing through a wedge-shaped die on a tensile machine has been developed to measure lubricant effectiveness.
One end of the strip is gripped and pulled through the die. The die may also be modified in order to simulate drawing over
draw beads. In these tests, resistance to sliding is measured for different lubricants applied to the strip.
Standard deep-drawing tests, such as the Swift cup test, can also be used to measure lubricant effectiveness. Poor surface
finish, score marks, or splits are indications of unsatisfactory lubrication. More information on tests for measuring the
drawability of metals is available in the article "Formability Testing of Sheet Metals" in this Volume; Ref 6 and 7 include
more details on evaluation of lubricant effectiveness. The larger the blanks formed and the deeper the cup, the more
effective the lubricant film. A wide variety of punch and sheet metal geometry, size, and tool material can be used along
with the lubricant coating. The limiting draw ratio (LDR) depends on the draw ratio (DR), which is equal to the ratio of
the blank diameter to the punch diameter. For a given punch diameter, the greater the blank diameter, the more severe the
operation. The LDR is the maximum DR that results in a satisfactory cup.