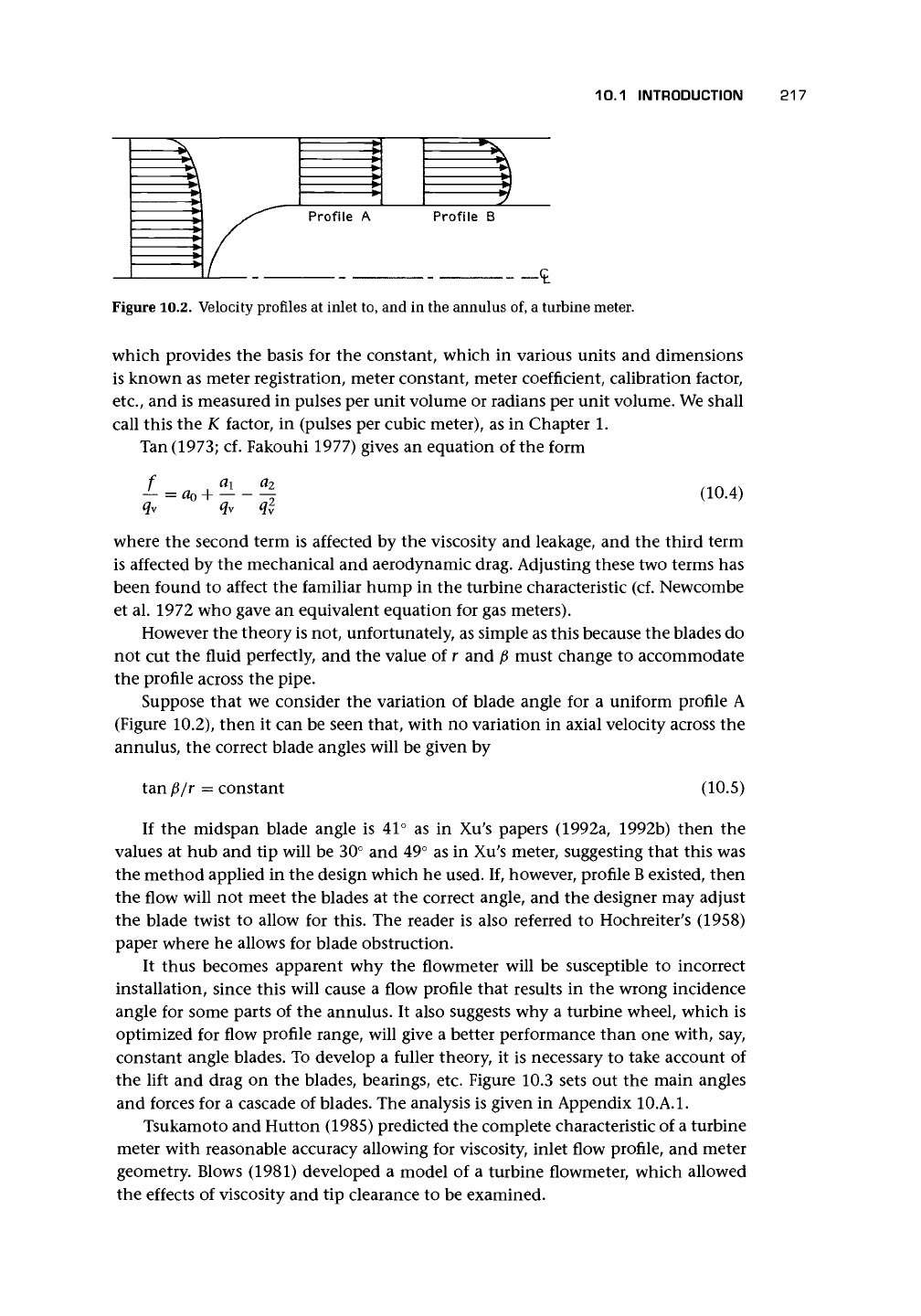
10.1
INTRODUCTION
217
Profile
A
Profile
B
<t
Figure
10.2.
Velocity profiles
at
inlet
to, and in the
annulus
of, a
turbine
meter.
which provides the basis for the constant, which in various units and dimensions
is known as meter registration, meter constant, meter coefficient, calibration factor,
etc.,
and is measured in pulses per unit volume or radians per unit volume. We shall
call this the K factor, in (pulses per cubic meter), as in Chapter 1.
Tan
(1973;
cf. Fakouhi 1977) gives an equation of the form
-*- = a
0
+
q
v
q
y
q*
(10.4)
where the second term is affected by the viscosity and leakage, and the third term
is affected by the mechanical and aerodynamic drag. Adjusting these two terms has
been found to affect the familiar hump in the turbine characteristic (cf. Newcombe
et al. 1972 who gave an equivalent equation for gas meters).
However the theory is not, unfortunately, as simple as this because the blades do
not cut the fluid perfectly, and the value of r and
/3
must change to accommodate
the profile across the pipe.
Suppose that we consider the variation of blade angle for a uniform profile A
(Figure 10.2), then it can be seen that, with no variation in axial velocity across the
annulus, the correct blade angles will be given by
tan/3/r = constant
(10.5)
If the midspan blade angle is 41° as in Xu's papers (1992a, 1992b) then the
values at hub and tip will be 30° and 49° as in Xu's meter, suggesting that this was
the method applied in the design which he used. If, however, profile
B
existed, then
the flow will not meet the blades at the correct angle, and the designer may adjust
the blade twist to allow for this. The reader is also referred to Hochreiter's (1958)
paper where he allows for blade obstruction.
It thus becomes apparent why the flowmeter will be susceptible to incorrect
installation, since this will cause a flow profile that results in the wrong incidence
angle for some parts of the annulus. It also suggests why a turbine wheel, which is
optimized for flow profile range, will give a better performance than one with, say,
constant angle blades. To develop a fuller theory, it is necessary to take account of
the lift and drag on the blades, bearings, etc. Figure 10.3 sets out the main angles
and forces for a cascade of blades. The analysis is given in Appendix
10.A.1.
Tsukamoto and Hutton (1985) predicted the complete characteristic of a turbine
meter with reasonable accuracy allowing for viscosity, inlet flow profile, and meter
geometry. Blows (1981) developed a model of a turbine flowmeter, which allowed
the effects of viscosity and tip clearance to be examined.