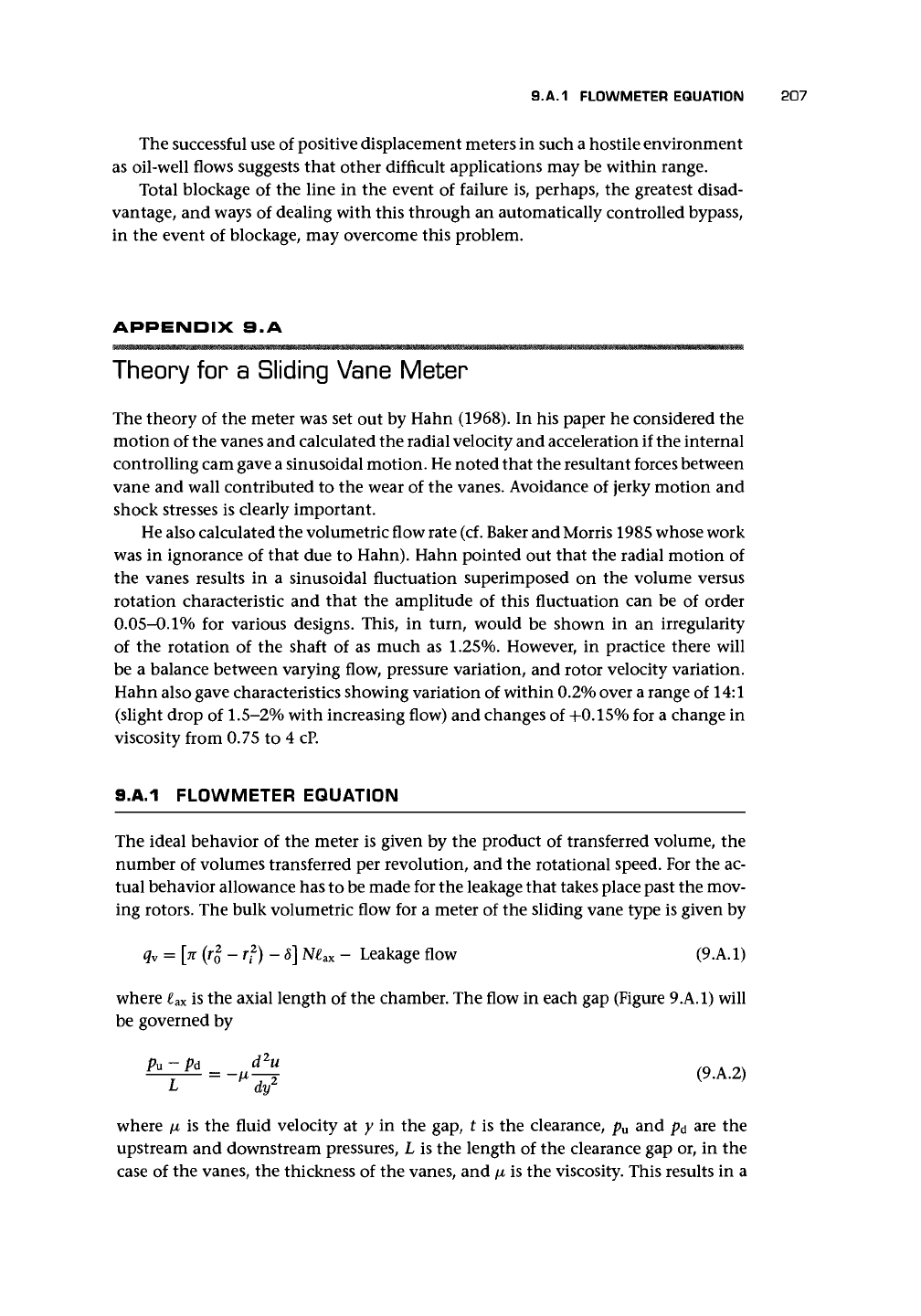
9.A.1 FLOWMETER EQUATION 207
The successful use of positive displacement meters in such a hostile environment
as oil-well flows suggests that other difficult applications may be within range.
Total blockage of the line in the event of failure is, perhaps, the greatest disad-
vantage, and ways of dealing with this through an automatically controlled bypass,
in the event of blockage, may overcome this problem.
APPENDIX
9.A
Theory for a Sliding Vane Meter
The theory of the meter was set out by Hahn (1968). In his paper he considered the
motion of the vanes and calculated the radial velocity and acceleration if the internal
controlling cam gave a sinusoidal motion. He noted that the resultant forces between
vane and wall contributed to the wear of the vanes. Avoidance of jerky motion and
shock stresses is clearly important.
He also calculated the volumetric flow rate (cf. Baker and Morris 1985 whose work
was in ignorance of that due to Hahn). Hahn pointed out that the radial motion of
the vanes results in a sinusoidal fluctuation superimposed on the volume versus
rotation characteristic and that the amplitude of this fluctuation can be of order
0.05-0.1%
for various designs. This, in turn, would be shown in an irregularity
of the rotation of the shaft of as much as
1.25%.
However, in practice there will
be a balance between varying flow, pressure variation, and rotor velocity variation.
Hahn also gave characteristics showing variation of within 0.2% over a range of 14:1
(slight drop of
1.5-2%
with increasing flow) and changes of +0.15% for a change in
viscosity from 0.75 to 4 cP.
9.A.1 FLOWMETER EQUATION
The ideal behavior of the meter is given by the product of transferred volume, the
number of volumes transferred per revolution, and the rotational speed. For the ac-
tual behavior allowance has to be made for the leakage that takes place past the mov-
ing rotors. The bulk volumetric flow for a meter of the sliding vane type is given by
q
y
= [n (r
0
2
- rf) -
8]
Nl
ax
- Leakage flow (9.A.I)
where £
ax
is the axial length of the chamber. The flow in each gap (Figure 9.A.I) will
be governed by
z
(9.A.2)
dy
where [i is the fluid velocity at y in the gap, t is the clearance, p
u
and pa are the
upstream and downstream pressures, L is the length of the clearance gap or, in the
case of the vanes, the thickness of the vanes, and
/JL
is the viscosity. This results in a