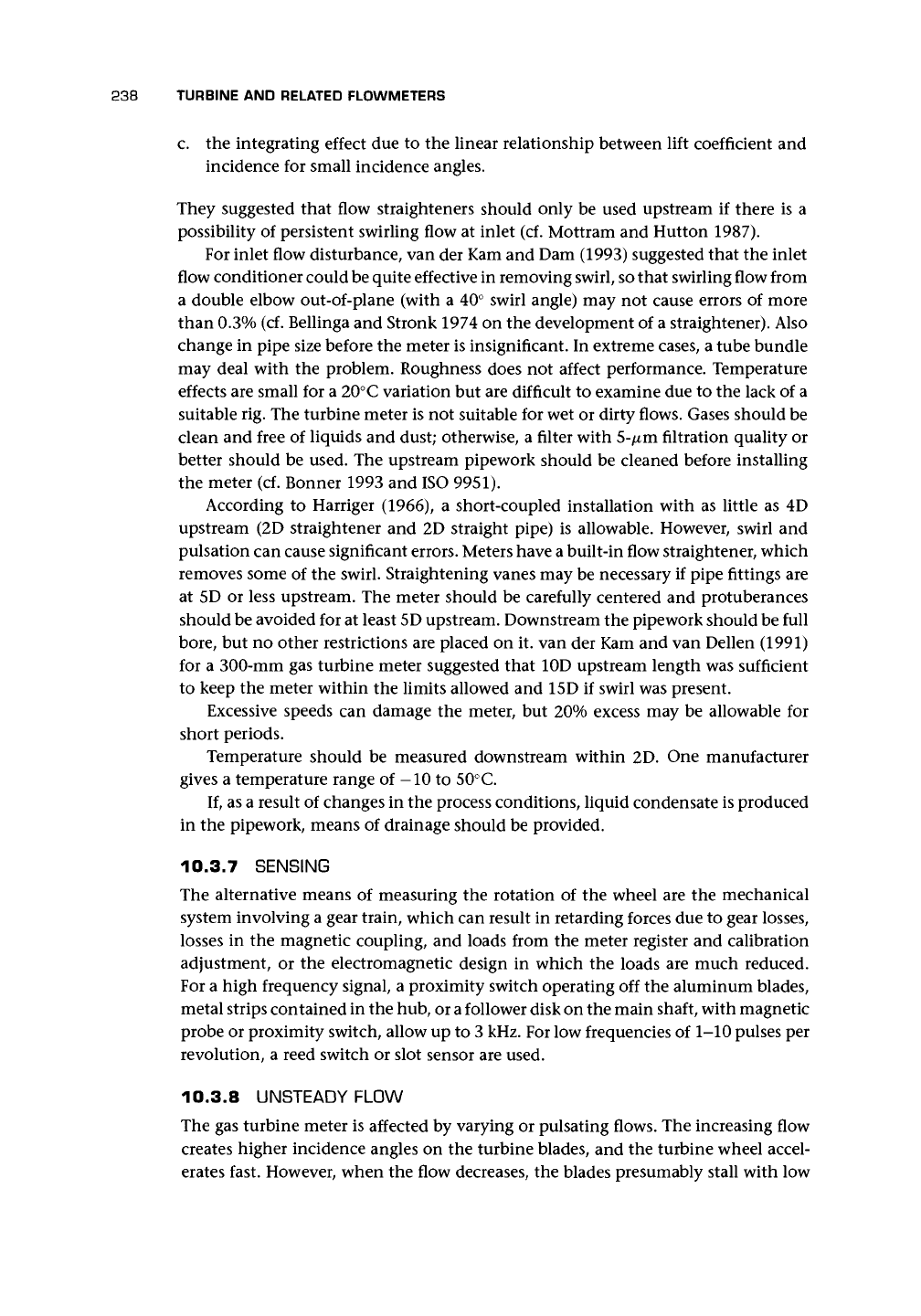
238 TURBINE AND RELATED FLOWMETERS
c. the integrating effect due to the linear relationship between lift coefficient and
incidence for small incidence angles.
They suggested that flow straighteners should only be used upstream if there is a
possibility of persistent swirling flow at inlet (cf. Mottram and Hutton 1987).
For inlet flow disturbance, van der Kam and Dam (1993) suggested that the inlet
flow conditioner could be quite effective in removing swirl, so that swirling flow from
a double elbow out-of-plane (with a 40° swirl angle) may not cause errors of more
than 0.3% (cf. Bellinga and Stronk 1974 on the development of a straightener). Also
change in pipe size before the meter is insignificant. In extreme cases, a tube bundle
may deal with the problem. Roughness does not affect performance. Temperature
effects are small for a 20° C variation but are difficult to examine due to the lack of a
suitable rig. The turbine meter is not suitable for wet or dirty flows. Gases should be
clean and free of liquids and dust; otherwise, a filter with 5-/xm filtration quality or
better should be used. The upstream pipework should be cleaned before installing
the meter (cf. Bonner 1993 and ISO 9951).
According to Harriger (1966), a short-coupled installation with as little as 4D
upstream (2D straightener and 2D straight pipe) is allowable. However, swirl and
pulsation can cause significant errors. Meters have
a
built-in flow straightener, which
removes some of the swirl. Straightening vanes may be necessary if pipe fittings are
at 5D or less upstream. The meter should be carefully centered and protuberances
should be avoided for at least 5D upstream. Downstream the pipework should be full
bore,
but no other restrictions are placed on it. van der Kam and van Dellen (1991)
for a 300-mm gas turbine meter suggested that 10D upstream length was sufficient
to keep the meter within the limits allowed and 15D if swirl was present.
Excessive speeds can damage the meter, but 20% excess may be allowable for
short periods.
Temperature should be measured downstream within 2D. One manufacturer
gives a temperature range of -10 to 50°C.
If, as a result of changes in the process conditions, liquid condensate is produced
in the pipework, means of drainage should be provided.
10.3.7 SENSING
The alternative means of measuring the rotation of the wheel are the mechanical
system involving a gear train, which can result in retarding forces due to gear losses,
losses in the magnetic coupling, and loads from the meter register and calibration
adjustment, or the electromagnetic design in which the loads are much reduced.
For a high frequency signal, a proximity switch operating off the aluminum blades,
metal strips contained in the hub, or a follower disk on the main shaft, with magnetic
probe or proximity switch, allow up to 3 kHz. For low frequencies of 1-10 pulses per
revolution, a reed switch or slot sensor are used.
10.3.8 UNSTEADY FLOW
The gas turbine meter is affected by varying or pulsating flows. The increasing flow
creates higher incidence angles on the turbine blades, and the turbine wheel accel-
erates fast. However, when the flow decreases, the blades presumably stall with low