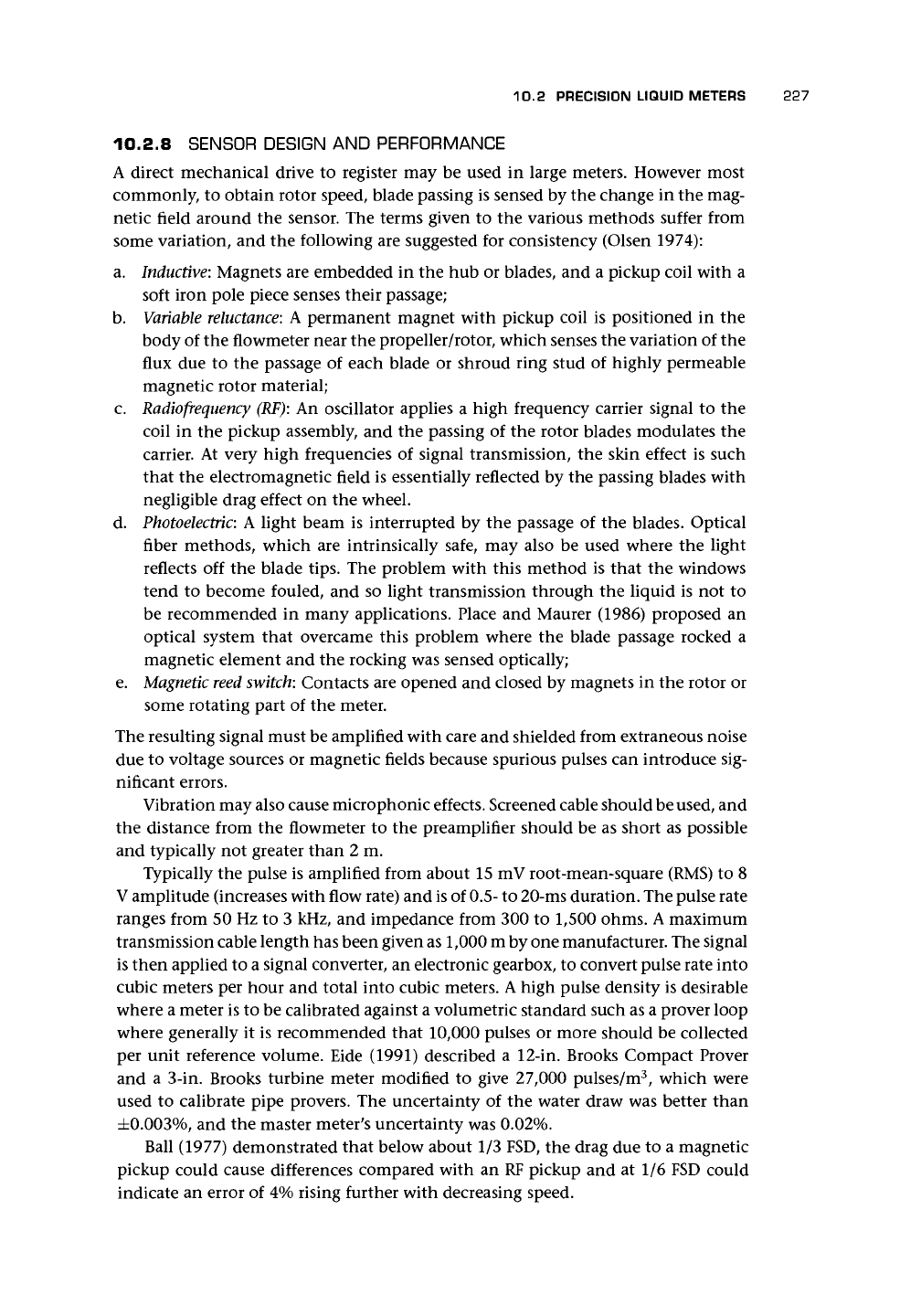
10.2 PRECISION LIQUID METERS 227
10.2.8 SENSOR DESIGN AND PERFORMANCE
A direct mechanical drive to register may be used in large meters. However most
commonly, to obtain rotor speed, blade passing is sensed by the change in the mag-
netic field around the sensor. The terms given to the various methods suffer from
some variation, and the following are suggested for consistency (Olsen 1974):
a.
Inductive:
Magnets are embedded in the hub or blades, and a pickup coil with a
soft iron pole piece senses their passage;
b.
Variable
reluctance:
A permanent magnet with pickup coil is positioned in the
body of the flowmeter near the propeller/rotor, which senses the variation of the
flux due to the passage of each blade or shroud ring stud of highly permeable
magnetic rotor material;
c.
Radiofrequency
(RF):
An oscillator applies a high frequency carrier signal to the
coil in the pickup assembly, and the passing of the rotor blades modulates the
carrier. At very high frequencies of signal transmission, the skin effect is such
that the electromagnetic field is essentially reflected by the passing blades with
negligible drag effect on the wheel.
d.
Photoelectric:
A light beam is interrupted by the passage of the blades. Optical
fiber methods, which are intrinsically safe, may also be used where the light
reflects off the blade tips. The problem with this method is that the windows
tend to become fouled, and so light transmission through the liquid is not to
be recommended in many applications. Place and Maurer (1986) proposed an
optical system that overcame this problem where the blade passage rocked a
magnetic element and the rocking was sensed optically;
e.
Magnetic reed
switch:
Contacts are opened and closed by magnets in the rotor or
some rotating part of the meter.
The resulting signal must be amplified with care and shielded from extraneous noise
due to voltage sources or magnetic fields because spurious pulses can introduce sig-
nificant errors.
Vibration may also cause microphonic effects. Screened cable should be used, and
the distance from the flowmeter to the preamplifier should be as short as possible
and typically not greater than 2 m.
Typically the pulse is amplified from about 15 mV root-mean-square (RMS) to 8
V
amplitude (increases with flow rate) and is of
0.5-
to 20-ms duration. The pulse rate
ranges from 50 Hz to 3 kHz, and impedance from 300 to 1,500 ohms. A maximum
transmission cable length has been given as 1,000 m by one manufacturer. The signal
is then applied to a signal converter, an electronic gearbox, to convert pulse rate into
cubic meters per hour and total into cubic meters.
A
high pulse density is desirable
where a meter is to be calibrated against a volumetric standard such as a prover loop
where generally it is recommended that 10,000 pulses or more should be collected
per unit reference volume. Eide (1991) described a 12-in. Brooks Compact Prover
and a 3-in. Brooks turbine meter modified to give 27,000 pulses/m
3
, which were
used to calibrate pipe provers. The uncertainty of the water draw was better than
±0.003%,
and the master meter's uncertainty was 0.02%.
Ball (1977) demonstrated that below about 1/3 FSD, the drag due to a magnetic
pickup could cause differences compared with an RF pickup and at 1/6 FSD could
indicate an error of 4% rising further with decreasing speed.