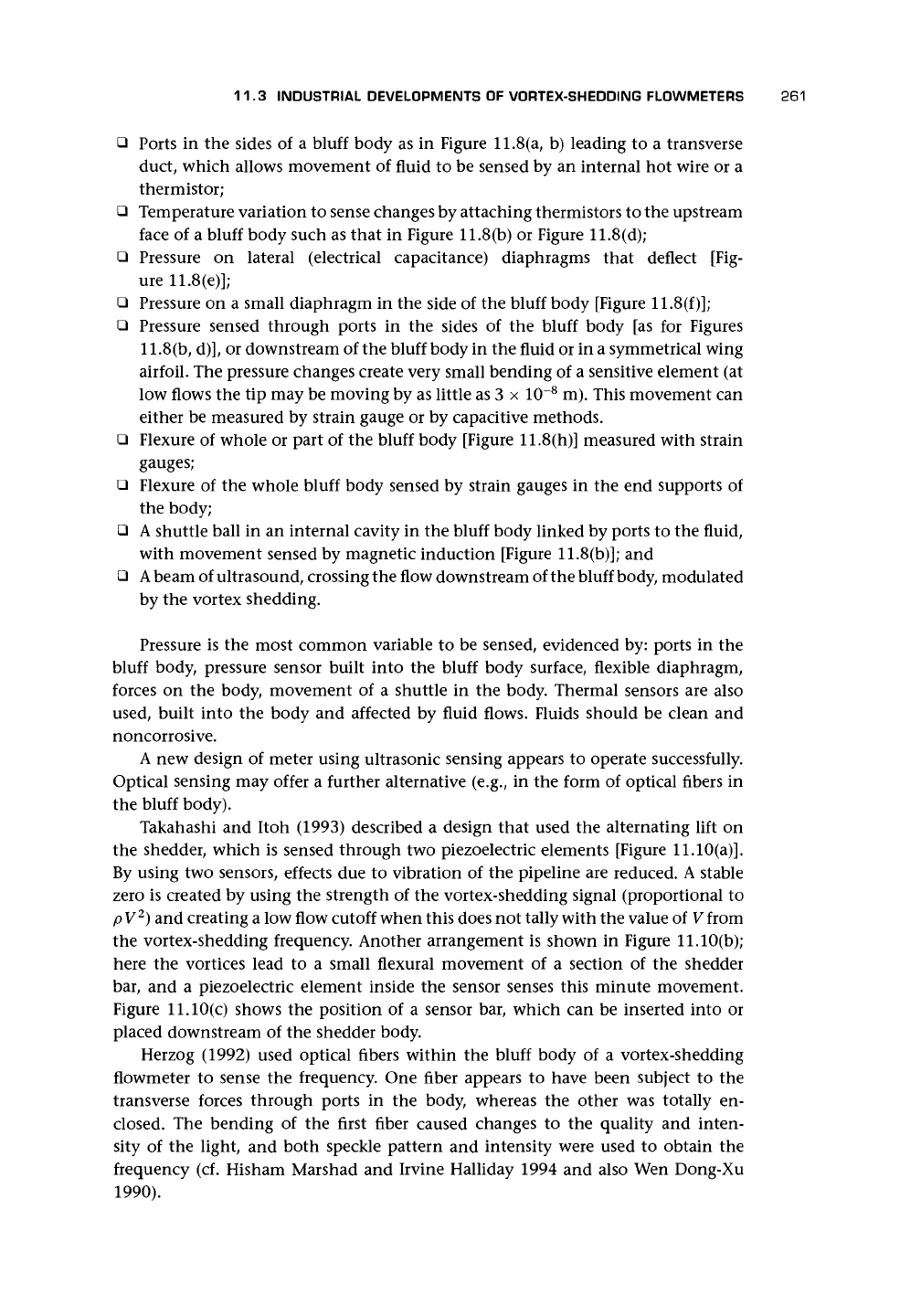
11.3 INDUSTRIAL DEVELOPMENTS OF VORTEX-SHEDDING FLOWMETERS 261
• Ports in the sides of a bluff body as in Figure 11.8 (a, b) leading to a transverse
duct, which allows movement of fluid to be sensed by an internal hot wire or a
thermistor;
• Temperature variation to sense changes by attaching thermistors to the upstream
face of a bluff body such as that in Figure 11.8(b) or Figure 11.8(d);
• Pressure on lateral (electrical capacitance) diaphragms that deflect [Fig-
ure 11.8(e)];
• Pressure on a small diaphragm in the side of the bluff body [Figure 11.8(f)];
• Pressure sensed through ports in the sides of the bluff body [as for Figures
11,8(b,
d)], or downstream of the bluff body in the fluid or in a symmetrical wing
airfoil. The pressure changes create very small bending of a sensitive element (at
low flows the tip may be moving by as little as 3 x 10~
8
m). This movement can
either be measured by strain gauge or by capacitive methods.
• Flexure of whole or part of the bluff body [Figure 11.8(h)] measured with strain
gauges;
• Flexure of the whole bluff body sensed by strain gauges in the end supports of
the body;
• A shuttle ball in an internal cavity in the bluff body linked by ports to the fluid,
with movement sensed by magnetic induction [Figure 11.8(b)]; and
•
A
beam of ultrasound, crossing the flow downstream of the bluff body, modulated
by the vortex shedding.
Pressure is the most common variable to be sensed, evidenced by: ports in the
bluff body, pressure sensor built into the bluff body surface, flexible diaphragm,
forces on the body, movement of a shuttle in the body. Thermal sensors are also
used, built into the body and affected by fluid flows. Fluids should be clean and
noncorrosive.
A new design of meter using ultrasonic sensing appears to operate successfully.
Optical sensing may offer a further alternative (e.g., in the form of optical fibers in
the bluff body).
Takahashi and Itoh (1993) described a design that used the alternating lift on
the shedder, which is sensed through two piezoelectric elements [Figure 11.10(a)].
By using two sensors, effects due to vibration of the pipeline are reduced. A stable
zero is created by using the strength of the vortex-shedding signal (proportional to
p
V
2
) and creating a low flow cutoff when this does not tally with the value of V from
the vortex-shedding frequency. Another arrangement is shown in Figure 11.10(b);
here the vortices lead to a small flexural movement of a section of the shedder
bar, and a piezoelectric element inside the sensor senses this minute movement.
Figure 11.10(c) shows the position of a sensor bar, which can be inserted into or
placed downstream of the shedder body.
Herzog (1992) used optical fibers within the bluff body of a vortex-shedding
flowmeter to sense the frequency. One fiber appears to have been subject to the
transverse forces through ports in the body, whereas the other was totally en-
closed. The bending of the first fiber caused changes to the quality and inten-
sity of the light, and both speckle pattern and intensity were used to obtain the
frequency (cf. Hisham Marshad and Irvine Halliday 1994 and also Wen Dong-Xu
1990).