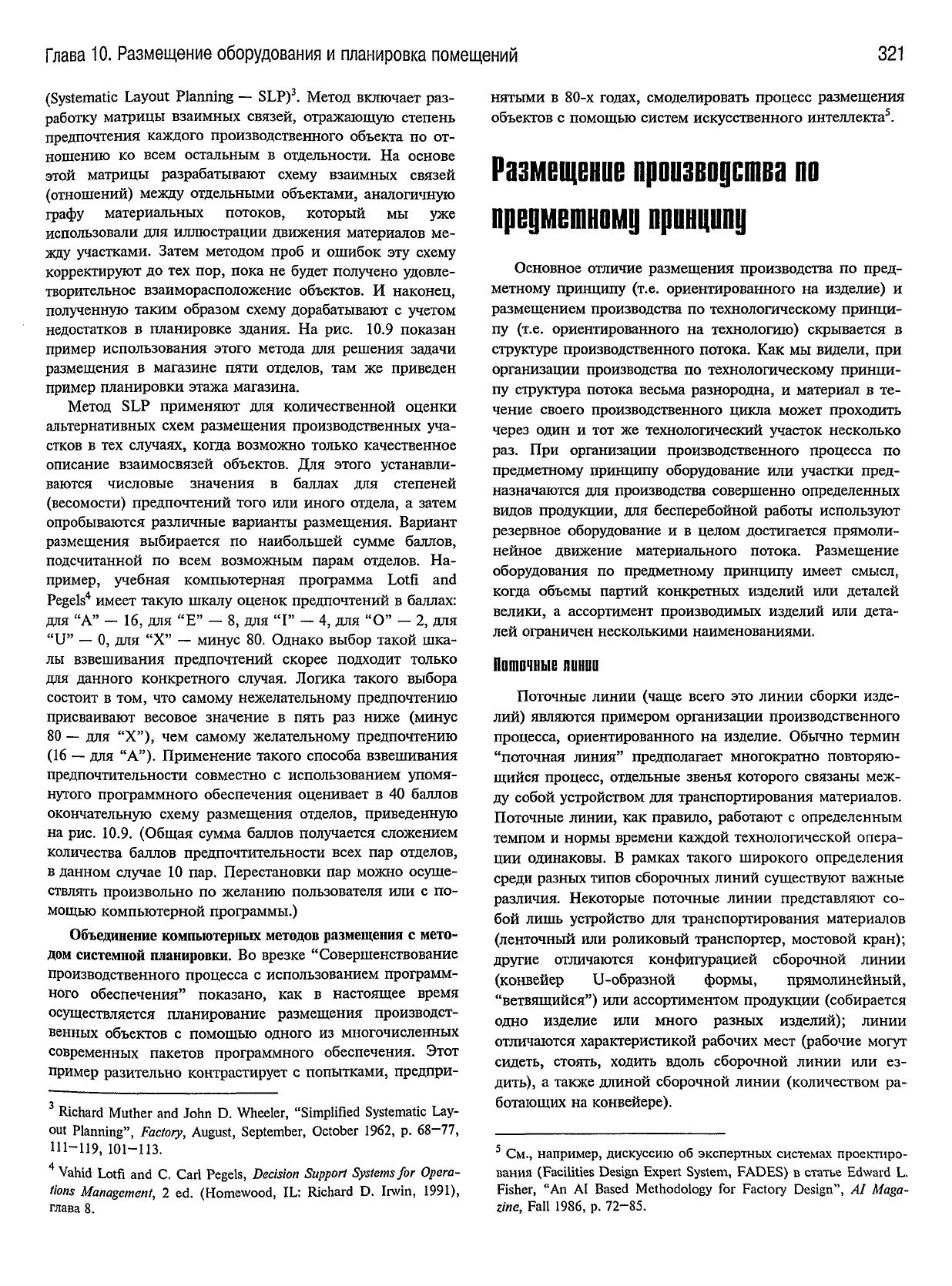
Глава
10. Размещение оборудования и планировка помещений
321
(Systematic Layout Planning — SLP)
3
. Метод включает раз-
работку матрицы взаимных связей, отражающую степень
предпочтения каждого производственного объекта по от-
ношению
ко всем остальным в отдельности. На основе
этой
матрицы разрабатывают
схему
взаимных связей
(отношений)
между
отдельными объектами, аналогичную
графу материальных потоков, который мы уже
использовали для иллюстрации движения материалов ме-
жду участками. Затем методом проб и ошибок эту
схему
корректируют до тех пор, пока не
будет
получено удовле-
творительное взаиморасположение объектов. И наконец,
полученную таким образом
схему
дорабатывают с
учетом
недостатков в планировке здания. На рис. 10.9 показан
пример использования этого метода для решения задачи
размещения
в магазине пяти отделов, там же приведен
пример планировки этажа магазина.
Метод SLP применяют для количественной оценки
альтернативных
схем
размещения производственных уча-
стков в тех
случаях,
когда возможно только качественное
описание
взаимосвязей объектов. Для этого устанавли-
ваются числовые значения в баллах для степеней
(весомости) предпочтений того или иного отдела, а затем
опробываются различные варианты размещения. Вариант
размещения
выбирается по наибольшей сумме баллов,
подсчитанной по всем возможным парам отделов. На-
пример,
учебная компьютерная программа Lotfi and
Pegels
4
имеет такую шкалу оценок предпочтений в
баллах:
для "А" - 16, для "Е" - 8, для "I" - 4, для "О" - 2, для
"U"
— 0, для "X" — минус 80. Однако выбор такой шка-
лы взвешивания предпочтений скорее подходит только
для данного конкретного случая. Логика такого выбора
состоит в том, что самому нежелательному предпочтению
присваивают весовое значение в пять раз ниже (минус
80 — для "X"), чем самому желательному предпочтению
(16 — для "А"). Применение такого способа взвешивания
предпочтительности совместно с использованием упомя-
нутого программного обеспечения оценивает в 40 баллов
окончательную
схему
размещения отделов, приведенную
на
рис. 10.9. (Общая сумма баллов получается сложением
количества баллов предпочтительности
всех
пар отделов,
в
данном
случае
10 пар. Перестановки пар можно осуще-
ствлять произвольно по желанию пользователя или с по-
мощью компьютерной программы.)
Объединение
компьютерных
методов
размещения
с
мето-
дом
системной
планировки.
Во врезке "Совершенствование
производственного процесса с использованием программ-
ного обеспечения" показано, как в настоящее время
осуществляется планирование размещения производст-
венных объектов с помощью одного из многочисленных
современных пакетов программного обеспечения. Этот
пример разительно контрастирует с попытками, предпри-
3
Richard Muther and John D.
Wheeler,
"Simplified
Systematic Lay-
out Planning",
Factory,
August,
September, October 1962, p.
68-77,
1П-119,
101-113.
4
Vahid
Lotfi and С Carl
Pegels,
Decision
Support
Systems
for
Opera-
tions
Management,
2 ed. (Homewood, IL: Richard D. Irwin,
1991),
глава 8.
нятыми
в 80-х
годах,
смоделировать процесс размещения
объектов с помощью систем искусственного интеллекта
5
.
Размещение
производства по
предметному принципу
Основное отличие размещения производства по пред-
метному принципу (т.е. ориентированного на изделие) и
размещением производства по технологическому принци-
пу (т.е. ориентированного на технологию) скрывается в
структуре
производственного потока. Как мы видели, при
организации
производства по технологическому принци-
пу
структура
потока весьма разнородна, и материал в те-
чение своего производственного цикла может проходить
через один и тот же технологический участок несколько
раз.
При организации производственного процесса по
предметному принципу оборудование или участки пред-
назначаются для производства совершенно определенных
видов продукции, для бесперебойной работы используют
резервное оборудование и в целом достигается прямоли-
нейное
движение материального потока. Размещение
оборудования по предметному принципу имеет смысл,
когда объемы партий конкретных изделий или деталей
велики,
а ассортимент производимых изделий или
дета-
лей ограничен несколькими наименованиями.
Поточные
линии
Поточные
ЛИНИИ
(чаще всего это
ЛИНИИ
сборки изде-
лий)
являются примером организации производственного
процесса, ориентированного на изделие. Обычно термин
"поточная
линия" предполагает многократно повторяю-
щийся
процесс, отдельные звенья которого связаны меж-
ду собой устройством для транспортирования материалов.
Поточные
линии, как правило, работают с определенным
темпом и нормы времени каждой технологической опера-
ции
одинаковы. В рамках такого широкого определения
среди разных типов сборочных линий
существуют
важные
различия.
Некоторые поточные линии представляют со-
бой лишь устройство для транспортирования материалов
(ленточный или роликовый транспортер, мостовой
кран);
другие
отличаются конфигурацией сборочной линии
(конвейер
U-образной формы, прямолинейный,
"ветвящийся") или ассортиментом продукции (собирается
одно изделие или много разных изделий); линии
отличаются характеристикой рабочих мест (рабочие
могут
сидеть, стоять, ходить вдоль сборочной линии или ез-
дить), а также длиной сборочной линии (количеством ра-
ботающих на конвейере).
См.,
например, дискуссию об экспертных системах проектиро-
вания
(Facilities Design Expert
System,
FADES) в
статье
Edward L.
Fisher, "An AI
Based
Methodology for Factory Design", AI
Maga-
zine,
Fall 1986, p. 72-85.