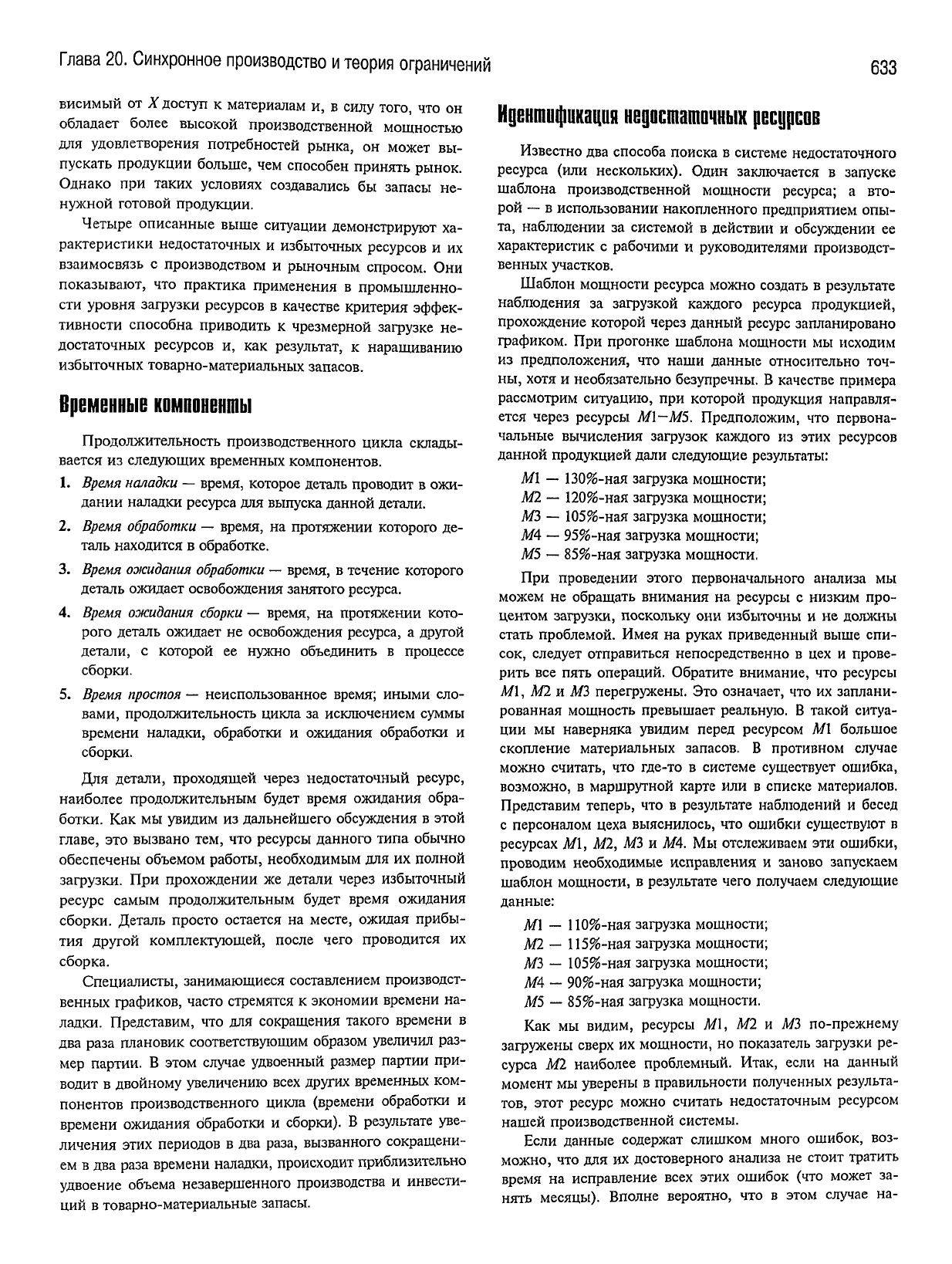
Глава
20. Синхронное производство
и
теория ограничений
633
висимый от X доступ к материалам и, в силу того, что он
обладает более высокой производственной мощностью
для удовлетворения потребностей рынка, он может вы-
пускать продукции больше, чем способен принять рынок.
Однако при таких условиях создавались бы запасы не-
нужной готовой продукции.
Четыре описанные выше ситуации демонстрируют ха-
рактеристики недостаточных и избыточных ресурсов и их
взаимосвязь с производством и рыночным спросом. Они
показывают, что практика применения в промышленно-
сти уровня загрузки ресурсов в качестве критерия
эффек-
тивности способна приводить к чрезмерной загрузке не-
достаточных ресурсов и, как результат, к наращиванию
избыточных товарно-материальных запасов.
Временные
компоненты
Продолжительность производственного цикла склады-
вается из следующих временных компонентов.
1.
Время
наладки
— время, которое деталь проводит в ожи-
дании наладки ресурса для выпуска данной детали.
2.
Время
обработки
— время, на протяжении которого де-
таль находится в обработке.
3.
Время
ожидания
обработки
— время, в течение которого
деталь ожидает освобождения занятого ресурса.
4.
Время
ожидания
сборки
— время, на протяжении кото-
рого деталь ожидает не освобождения ресурса, а другой
детали, с которой ее нужно объединить в процессе
сборки.
5.
Время
простоя
— неиспользованное время; иными сло-
вами, продолжительность цикла за исключением суммы
времени наладки, обработки и ожидания обработки и
сборки.
Для детали, проходящей через недостаточный ресурс,
наиболее продолжительным
будет
время ожидания обра-
ботки. Как мы увидим из дальнейшего обсуждения в этой
главе, это вызвано тем, что ресурсы данного типа обычно
обеспечены объемом работы, необходимым для их полной
загрузки. При прохождении же детали через избыточный
ресурс самым продолжительным
будет
время ожидания
сборки.
Деталь просто остается на месте, ожидая прибы-
тия
другой комплектующей, после чего проводится их
сборка.
Специалисты, занимающиеся составлением производст-
венных графиков, часто стремятся к экономии времени на-
ладки. Представим, что для сокращения такого времени в
два раза плановик соответствующим образом увеличил раз-
мер партии. В этом
случае
удвоенный размер партии при-
водит в двойному увеличению всех
других
временных ком-
понентов производственного цикла (времени обработки и
времени ожидания обработки и сборки). В результате уве-
личения
этих периодов в два раза, вызванного сокращени-
ем в два раза времени наладки, происходит приблизительно
удвоение объема незавершенного производства и инвести-
ций
в товарно-материальные запасы.
Идентификация
недостаточных
ресурсов
Известно два способа поиска в системе недостаточного
ресурса (или нескольких). Один заключается в запуске
шаблона производственной мощности ресурса; а вто-
рой — в использовании накопленного предприятием опы-
та, наблюдении за системой в действии и обсуждении ее
характеристик с рабочими и руководителями производст-
венных участков.
Шаблон
мощности ресурса можно создать в результате
наблюдения за загрузкой каждого ресурса продукцией,
прохождение которой через данный ресурс запланировано
графиком.
При прогонке шаблона мощности мы исходим
из
предположения, что наши данные относительно точ-
ны,
хотя и необязательно безупречны. В качестве примера
рассмотрим ситуацию, при которой продукция направля-
ется через ресурсы М1-М5. Предположим, что первона-
чальные вычисления загрузок каждого из этих ресурсов
данной продукцией дали следующие результаты:
Л/1 — 130%-ная загрузка мощности;
Л/2 — 120%-ная загрузка мощности;
Л/3 — 105%-ная загрузка мощности;
Л/4 — 95%-ная загрузка мощности;
Л/5 — 85%-ная загрузка мощности.
При
проведении этого первоначального анализа мы
можем не обращать внимания на ресурсы с низким про-
центом загрузки, поскольку они избыточны и не должны
стать проблемой. Имея на руках приведенный выше спи-
сок,
следует
отправиться непосредственно в цех и прове-
рить все пять операций. Обратите внимание, что ресурсы
Л/1,
Ml и
МЪ
перегружены. Это означает, что их заплани-
рованная
мощность превышает реальную. В такой ситуа-
ции
мы наверняка увидим перед ресурсом М\ большое
скопление материальных запасов. В противном
случае
можно считать, что
где-то
в системе
существует
ошибка,
возможно, в маршрутной карте или в списке материалов.
Представим теперь, что в результате наблюдений и бесед
с персоналом цеха выяснилось, что ошибки
существуют
в
ресурсах Ml, Ml, МЪ и Л/4. Мы отслеживаем эти ошибки,
проводим необходимые исправления и заново запускаем
шаблон мощности, в результате чего получаем следующие
данные:
Ml — 110%-ная загрузка мощности;
Ml — 115%-ная загрузка мощности;
МЪ
— 105%-ная загрузка мощности;
Л/4 — 90%-ная загрузка мощности;
Л/5 — 85%-ная загрузка мощности.
Как
мы видим, ресурсы Л/1, Л/2 и Л/3 по-прежнему
загружены сверх их мощности, но показатель загрузки ре-
сурса Ml наиболее проблемный. Итак, если на данный
момент мы уверены в правильности полученных результа-
тов, этот ресурс можно считать недостаточным ресурсом
нашей
производственной системы.
Если данные содержат слишком много ошибок, воз-
можно,
что для их достоверного анализа не стоит тратить
время на исправление всех этих ошибок (что может за-
нять
месяцы). Вполне вероятно, что в этом
случае
на-