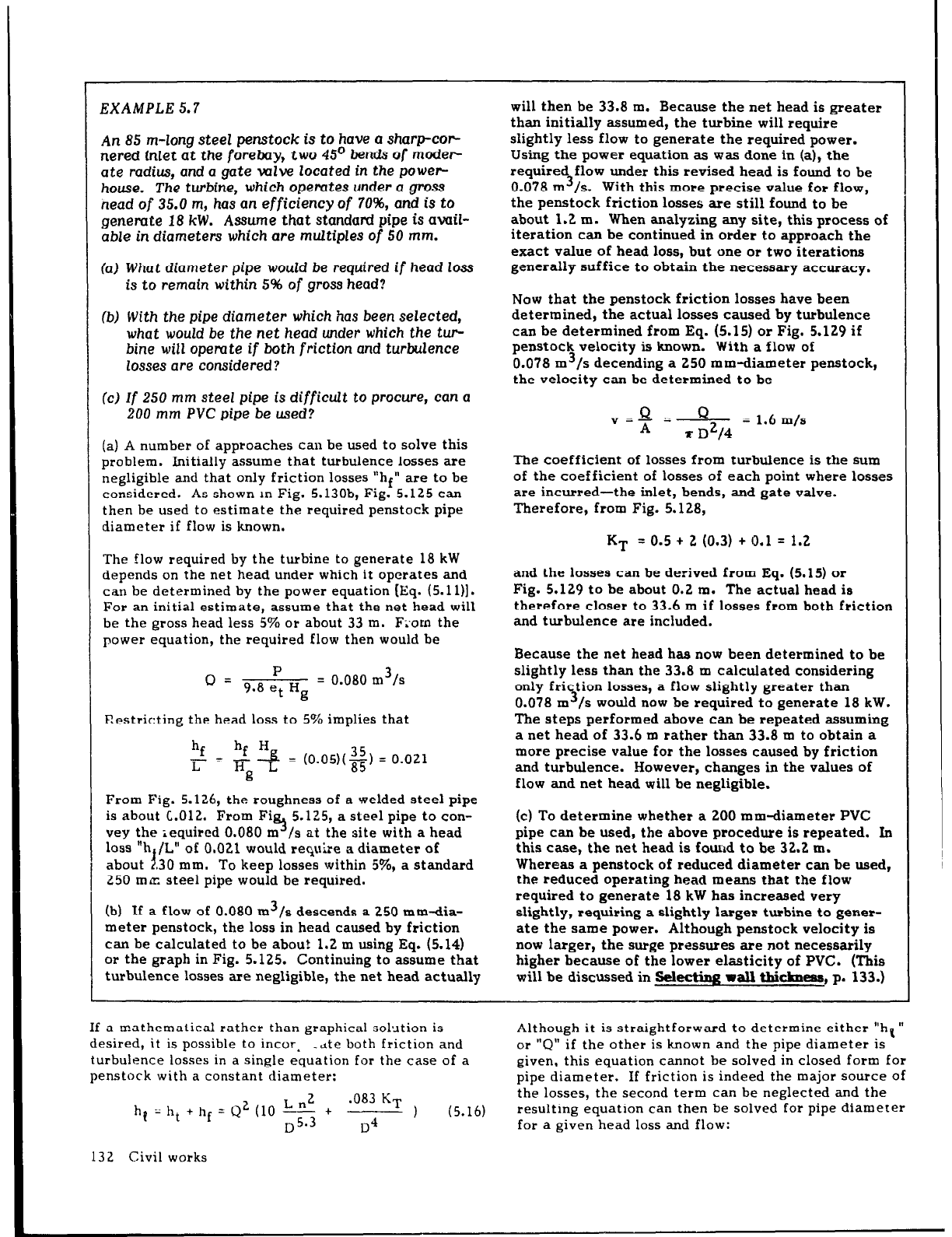
1
EXAMPLE 5.7
An 85
m-long steel penstock is to have
a
sharp-cor-
nered inlet at the forebay, two 45’ bends of moder-
ate radius, and
a gate
valve located
in the power-
house. The
turbine,
which operates under a gross
nead of 35.0
m, has an
efficiency of 70%, and is to
genemte 18 kW. Assume that standard pipe is awil-
able in
diameters
which are
multiples
of
50
mm.
(a)
What diameter pipe wouEd
be required if head loss
is to remain within 5%
of gross
head?
(b) With the pipe diameter which
has been
selected,
what would be the net head
under
which the tur-
bine
will
operate
if
both friction
and turbulence
losses are considered?
Cc) If 250 mm steel pipe is
difficult
to procure, can a
200 mm PVC pipe be used?
(a) A number of approaches can be used to solve this
problem. Initially assume that turbulence losses are
negligible and that only friction losses “hf” are to be
considered. As shown in Fig. 5.130b, Fig. 5.125 can
then be used to estimate the required penstock pipe
diameter if flow is known.
The flow required by the turbine to generate 18 kW
depends on the net head under which it operates and
can be determined by the power equation (Eq. (5.11)].
For an initial estimate, assume that the net head will
be the gross head less 5% or about 33 m. F:om the
power equation, the required flow then would be
P
Q = 9,8 et Hg = 0.080 m3/s
Restricting the head loss to 5% implies that
h f hf 2
-=-
L H
Iii L
= (0.05)(g) = 0.021
From Fig. 5.126, the roughness of a welded steel pipe
is about C.012. From Fi
q 5.125, a steel pipe to con-
vey the required 0.080 m /s at the site with a head
loss “h /L” of 0.021 would
reyGre
a diameter of
about 4 -30 mm. To keep losses within 5%, a standard
250 ma: steel pipe would be required.
(b) If a flow of 0.080 m3/s descends a 250 mm-dia-
meter penstock, the loss in head caused by friction
can be calculated to be about 1.2 m using Eq. (5.14)
or the graph in Fig. 5.125. Continuing to assume that
turbulence losses are negligible, the net head actually
will then be 33.8 m. Because the net head is greater
than initially assumed, the turbine will require
slightly less flow to generate the required power.
Using the power equation as was done in (a), the
required flow under this revised head is found to be
0.078 m3/s. With this more precise value for flow,
the penstock friction losses are still found to be
about 1.2 m. When analyzing any site, this process of
iteration can be continued in order to approach the
exact value of head loss, but one or two iterations
generally suffice to obtain the necessary accuracy.
Now that the penstock friction losses have been
determined, the actual losses caused by turbulence
can be determined from Eq. (5.15) or Fig. 5.129 if
penstock velocity is known. With a flow of
0.078 m3/s decending a 250 mm-diameter penstock,
the velocity can be determined to be
Q Q
v =-
A
= - = 1.6 m/s
z D2/4
The coefficient of losses from turbulence is the sum
of the coefficient of losses of each point where losses
are incurred-the inlet, bends, and gate valve.
Therefore, from Fig. 5.128,
KT = 0.5 t 2 (0.3) + 0.1 = 1.2
and the losses can be derived from Eq. (5.15)
or
Fig. 5.129 to be about 0.2 m. The actual head is
therefore closer to 33.6 m if losses from both friction
and turbulence are included.
Because the net head has
now
been determined to be
slightly less than the 33.8 m calculated considering
only fri tion losses, a flow slightly greater than
5
0.078 m /s would now be required to generate 18 kW.
The steps performed above can be repeated assuming
a net head of 33.6 m rather than 33.8 m to obtain a
more precise value for the losses caused by friction
and turbulence. However, changes in the values of
flow and net head will be negligible.
(c) To determine whether a 200 mm-diameter PVC
pipe can be used, the above procedure is repeated. In
this case, the net head is found to be 32.2 m.
Whereas a penstock of reduced diameter can be used,
the reduced operating head means that the flow
required to generate 18 kW has increased very
slightly, requiring a slightly larger turbine to gener-
ate the same power. Although penstock velocity is
now larger, the surge pressures are not necessarily
higher because of the lower elasticity of PVC. (This
will be discussed in Selecting rail thicknw, p. 133.)
If a mathematical rather than graphical sol*ltion is
Although it is straightforward to determine either “h( It
desired, it is possible to incor. -dte both friction and
or “Q” if the other is known and the pipe diameter is
turbulence losses in a single equation for the case of a
given, this equation cannot be solved in closed form for
penstock with a constant diameter:
pipe diameter. If friction is indeed the major source
of
the losses, the second term can be neglected and the
ht = ht + hf = Q
(5.16)
resulting equation can then be solved for pipe diameter
for a given head loss and flow:
132 Civil works