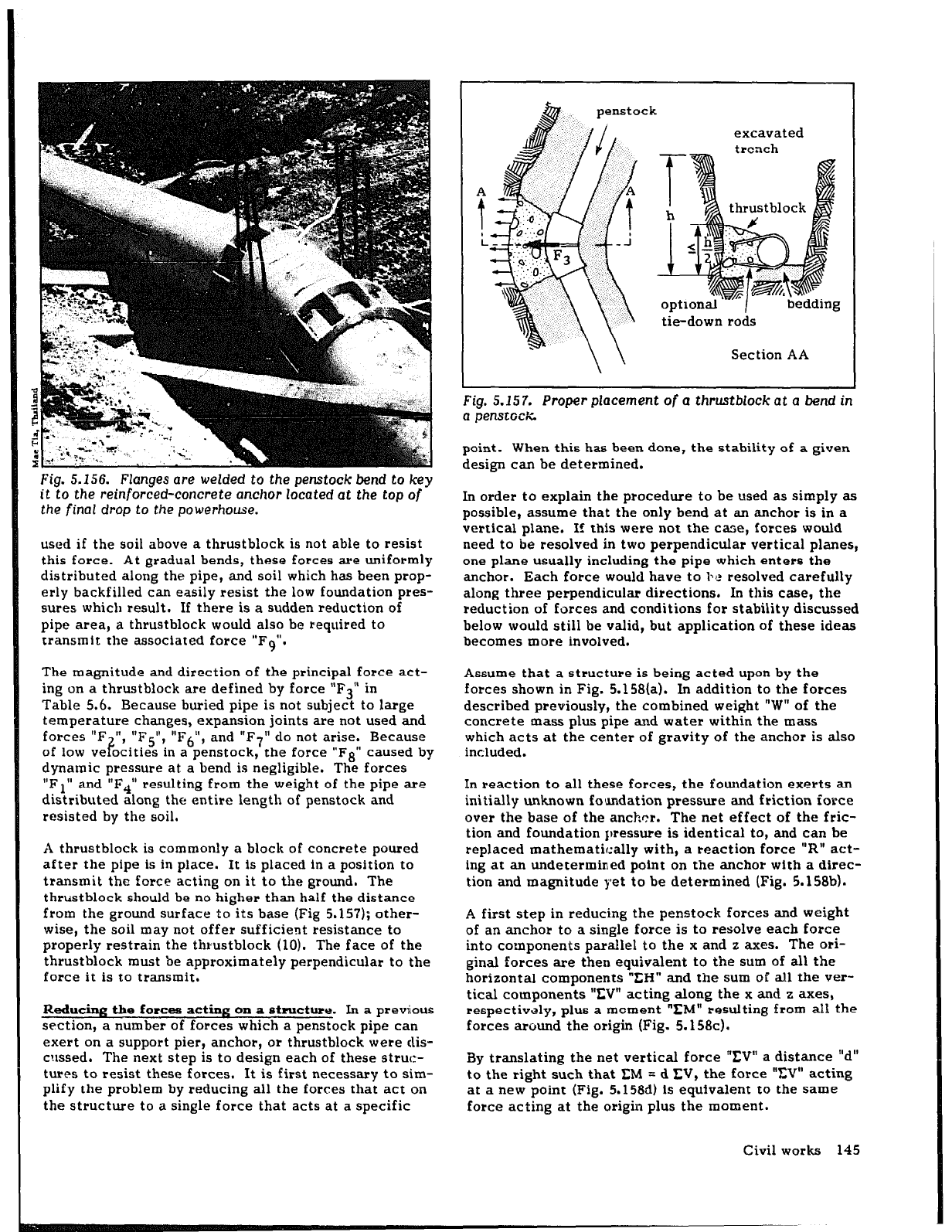
Fig. 5.156. Flanges are welded to the penstock bend to key
it
to
the
reinforced-concrete anchor located
at
the top
of
the final drop to the powerhouse.
used if the soil above a thrustblock is not able to resist
this force. At gradual bends, these forces are uniformly
distributed along the pipe, and soil which has been prop-
erly backfilled can easily resist the low foundation pres-
sures which result. If there is a sudden reduction of
pipe area, a thrustblock would also be required to
transmit the associated force “F9”.
The magnitude and direction of the principal force act-
ing on a thrustblock are defined by force “F3” in
Table 5.6. Because buried pipe is not subject to large
temperature changes, expansion joints are not used and
forces “F
of low
“, “F5”, “F6”, and “F7” do not arise. Because
ve ocities in a penstock, the force “Fs” caused by F
dynamic pressure at a bend is negligible. The forces
“Fl” and “F4” resulting from the weight of the pipe are
distributed along the entire length of penstock and
resisted by the soil.
A thrustblock is commonly a block of concrete poured
after the pipe is
in
place. It is placed in a position to
transmit the force acting on it to the ground. The
thrustblock should be no higher than half the distance
from the ground surface to its base (Fig 5.157); other-
wise, the soil may not offer sufficient resistance to
properly restrain the thrustblock (10). The face of the
thrustblock must be approximately perpendicular to the
force it is to transmit.
Reducing the forces acting on a structure. In a previous
section, a number of forces which a penstock pipe can
exert on a support pier, anchor, or thrustblock were dis-
cussed. The next step is to design each of these struc-
tures to resist these forces. It is first necessary to sim-
plify the problem by reducing all the forces that act on
the structure to a single force that acts at a specific
excavated
trench
tie-down rods
Section AA
Fig. 5.157. Proper placement
of
a thrustblock at a bend in
a penstock
point. When this has been done, the stability of a given
design can be determined.
In order to explain the procedure to be used as simply as
possible, assume that the only bend at an anchor is in a
vertical plane. If this were not the case, forces would
need to be resolved in two perpendicular vertical planes,
one plane usually including the pipe which enters the
anchor. Each force would have to bc resolved carefully
along three perpendicular directions. In this case, the
reduction of forces and conditions for stability discussed
below would still be valid, but application of these ideas
becomes more involved.
Assume that a structure is being acted upon by the
forces shown in Fig. 5.158(a). In addition to the forces
described previously, the combined weight “W” of the
concrete mass plus pipe and water within the mass
which acts at the center of gravity of the anchor is also
included.
In reaction to all these forces, the foundation exerts an
initially unknown foundation pressure and friction force
over the base of the anchor. The net effect of the fric-
tion and foundation pressure is identical to, and can be
replaced mathematically with, a reaction force “R” act-
ing at an undetermined point on the anchor with a direc-
tion and magnitude yet to be determined (Fig. 5.158bl.
A first step in reducing the penstock forces and weight
of an anchor to a single force is to resolve each force
into components parallel to the x and z axes. The ori-
ginal forces are then equivalent to the sum of all the
horizontal components “EIi” and the sum of all the ver-
tical components ‘ZV” acting along the x and z axes,
respectively, plus a moment “EM” resulting from all the
forces around the origin (Fig. 5.158~).
By translating the net vertical force “EV” a distance “d”
to the right such that
CM
= d IX, the force ‘?X” acting
at a new point (Fig. 5.1586) is equivalent to the same
force acting at the origin plus the moment.
Civil works 145