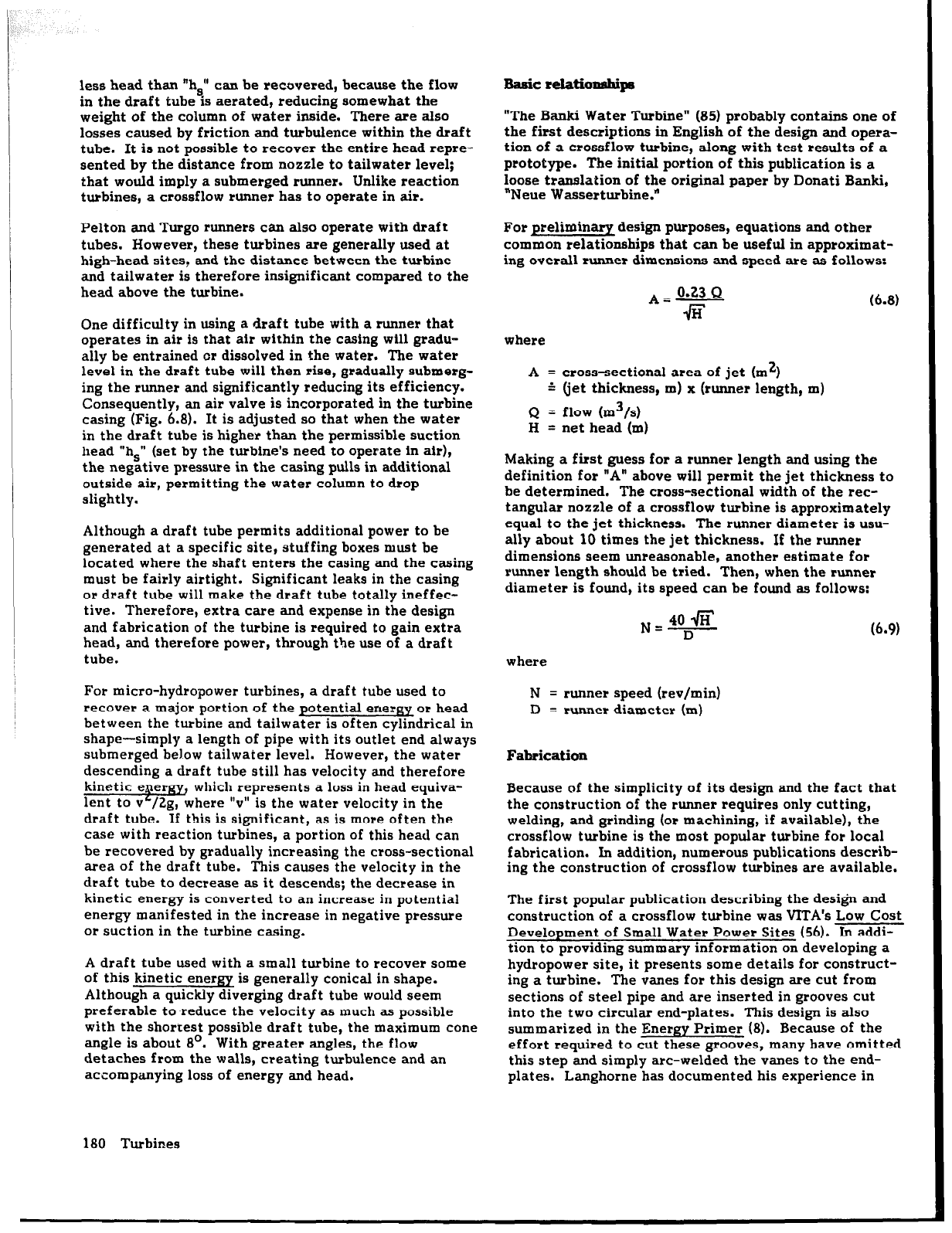
less head than “hs” can be recovered, because the flow
in the draft tube is aerated, reducing somewhat the
weight of the column of water inside. There are also
losses caused by friction and turbulence within the draft
tube. It is not possible to recover the entire head repre-
sented by the distance from nozzle to tailwater level;
that would imply a submerged runner. Unlike reaction
turbines, a crossflow runner has to operate in air.
Pelton and Turgo runners can also operate with draft
tubes. However, these turbines are generally used at
high-head sites, and the distance between the turbine
and tailwater is therefore insignificant compared to the
head above the turbine.
One difficulty in using a draft tube with a runner that
operates in air is that air within the casing will gradu-
ally be entrained or dissolved in the water. The water
level in the draft tube will then rise, gradually submerg-
ing the runner and significantly reducing its efficiency.
Consequently, an air valve is incorporated in the turbine
casing (Fig.
6.8).
It is adjusted so that when the water
in the draft tube is higher than the permissible suction
head “hS” (set by the turbine’s need to operate in air),
the negative pressure in the casing pulls in additional
outside air, permitting the water column to drop
slightly.
Although a draft tube permits additional power to be
generated at a specific site, stuffing boxes must be
located where the shaft enters the casing and the casing
must be fairly airtight. Significant leaks in the casing
or draft tube will make the draft tube totally ineffec-
tive. Therefore, extra care and expense in the design
and fabrication of the turbine is required to gain extra
head, and therefore power, through the use
of
a draft
tube.
For micro-hydropower turbines, a draft tube used to
recover a major portion of the potential energy or head
between the turbine and tailwater is often cvlindrical in
shape-simply a length of pipe with its outlet end always
submerged below tailwater level. However, the water
descending a draft tube still has velocity and therefore
kinetic epergy, which represents a loss in head equiva-
lent to v‘/2g, where “v” is the water velocity in the
draft tube. If this is significant, as is more often the
case with reaction turbines, a portion of this head can
be recovered by gradually increasing the cross-sectional
area of the draft tube. This causes the velocity in the
draft tube to decrease as it descends; the decrease in
kinetic energy is converted to an increase in potential
energy manifested in the increase in negative pressure
or suction in the turbine casing.
A draft tube used with a small turbine to recover some
of this kinetic enerm is generally conical in shape.
Although a quickly diverging draft tube would seem
preferable to -reduce the velocity as much as possible
with the shortest possible draft tube, the maximum cone
angle is about 8’.
With greater angles, the flow
detaches from the walls, creating turbulence and an
accompanying loss of energy and head.
Basic relat.iolIships
“The Banki Water Turbine” (85) probably contains one of
the first descriptions in English of the design and opera-
tion of a crossflow turbine, along with test results of a
prototype. The initial portion of this publication is a
loose translation of the original paper by Donati Banki,
“Neue Wasserturbiie.”
For preliminq design purposes, equations and other
common relationships that can be useful in approximat-
ing overall runner dimensions and speed are as follows:
(6.8)
where
A = cross-sectional area of jet (m2)
s (jet thickness, m) x (runner length, m)
Q = flow (m3/s)
H = net head (m)
Making a first guess for a runner length and using the
definition for “A” above will permit the jet thickness to
be determined. The cross-sectional width
of
the
rec-
tangular nozzle of a crossflow turbine is approximately
equal to the jet thickness. The runner diameter is usu-
ally about 10 times the jet thickness. If the runner
dimensions seem unreasonable, another estimate for
runner length should be tried. Then, when the runner
diameter is found, its speed can be found as follows:
where
N = runner speed (rev/min)
D = runner diameter (m)
Fabrication
Because of the simplicity of its design and the fact that
the construction
of
the runner requires only cutting,
welding, and grinding (or machining, if available), the
crossflow turbine is the most popular turbine for local
fabrication. In addition, numerous publications describ-
ing the construction of crossflow turbines are available.
The first popular publication describing the desi@ and
construction of a crossflow turbine was VITA’s Low Cost
Development of Small Water Power Sites (56). In addi-
tion to providing summary information on developing a
hydropower site, it presents some details for construct-
ing a turbine. The vanes for this design are cut from
sections of steel pipe and are inserted in grooves cut
into the two circular end-plates. This design is also
summarized in the Energy Primer (8). Because of the
effort required to cut these grooves, many have omitted
this step and simply arc-welded the vanes to the end-
plates. Langhorne has documented his experience in
180 Turbines