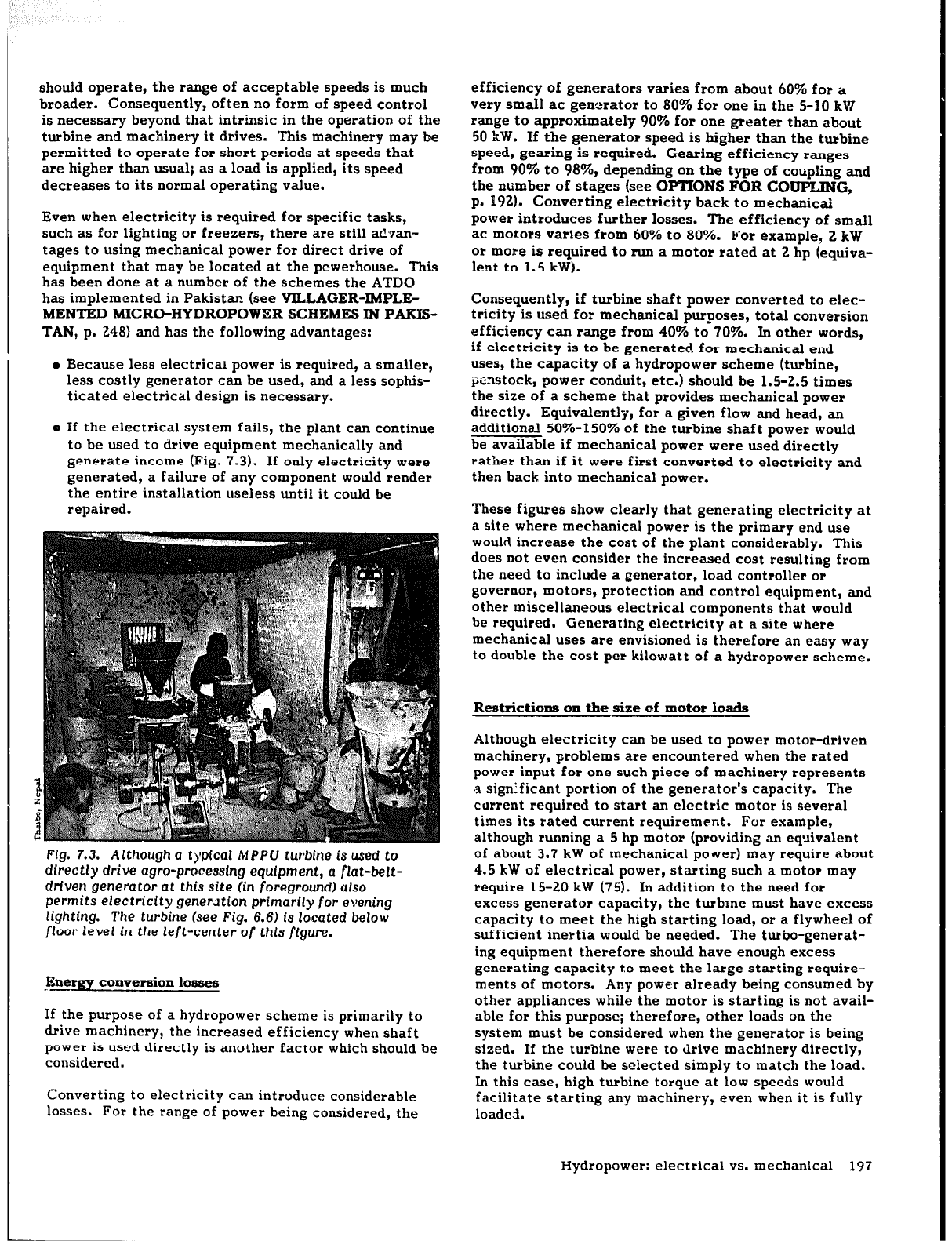
should operate, the range of acceptable speeds is much
broader. Consequently, often no form of speed control
is necessary beyond that intrinsic in the operation of the
turbine and machinery it drives. This machinery may be
permitted to operate for short periods at speeds that
are higher than usual; as a load is applied, its speed
decreases to its normal operating value.
Even when electricity is required for specific tasks,
such as for lighting or freezers, there are still adoan-
tages to using mechanical power for direct drive of
equipment that may be located at the pcwerhouse. This
has been done at a number of the schemes the ATDO
has implemented in Pakistan (see
WTLLAGER-IMPLE-
MENTED MICRO-HYDROPOWER SCHEMES IN PAlUS-
TAN,
p. 248) and has the following advantages:
o Because less electrical power is required, a smaller,
less costly generator can be used, and a less sophis-
ticated electrical design is necessary.
o If the electrical system fails, the plant can continue
to be used to drive equipment mechanically and
generate income (Fig. 7.3). If only electricity
were
generated, a failure of any component would render
the entire installation useless until it could be
repaired.
Fig. 7.3. Although
a typkal MPPU turbine is used to
directly drive agro-processing equfpment,
a flat-belt-
driven genemtor at this site (in foreground) also
permits electricity
genehltlon prfmarily for evening
Ilghting. The turbine (see Fig. 6.61 is located below
floor level in the left-center of this
figure.
~
Energy conversion losses
.-
If the purpose of a hydropower scheme is primarily to
drive machinery, the increased efficiency when shaft
power is used directly is another factor which should be
considered.
Converting to electricity can introduce considerable
losses. For the range of power being considered, the
efficiency of generators varies from about 60% for a
very small ac generator to 80% for one in the S-10 kW
range
to approximately 90% for one greater than about
50 kW. If the generator speed is higher than the turbine
speed, gearing is required. Gearing efficiency ranges
from 90% to 98%, depending on the type of coupling and
the number of stages (see OPTIONS
FOR COUPLING,
p. I92). Converting electricity back to mechanicaI
power introduces further losses. The efficiency of small
ac motors varies from 60% to 80%. For example, 2 kW
or more is required to run a motor rated at 2 hp (equiva-
lent to 1.5 kW).
Consequently, if turbine shaft power converted to elec-
tricity is used for mechanical purposes, total conversion
efficiency can range from 40% to 70%. In other words,
if electricity is to be generated for mechanical end
uses, the capacity of a hydropower scheme (turbine,
pienstock, power conduit, etc.) should be 1.5-2.5 times
the size of a scheme that provides mechanical power
directly. Equivalentlyy,
for
a given flow and head, an
additional 50%-150% of the turbine shaft power would
be available if mechanical power were used directly
rather than if it were first converted to electricity and
then back into mechanical power.
These figures show clearly that generating electricity at
a site where mechanical power is the primary end use
would increase the cost of the plant considerably. This
does not even consider the increased cost resulting
from
the need to include a generator, load controller
or
governor, motors, protection and control equipment, and
other miscellaneous electrical components that would
be required. Generating electricity at a site where
mechanical uses are envisioned is therefore an easy way
to double the cost per kilowatt of a hydropower scheme.
Restrictions on the size of motor loads
Although electricity can be used to power motor-driven
machinery, problems are encountered when the rated
power input for one such piece of machinery represents
,a significant portion of the generator’s capacity. The
current required to start an electric motor is several
times its rated current requirement. For example,
although running a 5 hp motor (providing an equivalent
of about 3.7 kW of mechanical power) may require about
4.5 kW of electrical power, starting such a motor may
require 15-20 kW (75). In addition to the need for
excess generator capacity, the turbine must have excess
capacity to meet the high starting load, or a flywheel of
sufficient inertia would be needed. The turbo-generat-
ing equipment therefore should have enough excess
generating capacity to meet the large starting require-
ments of motors. Any power already being consumed by
other appliances while the motor is starting is not avail-
able for this purpose; therefore, other loads on the
system must be considered when the generator is being
sized. If the turbine were to drive machinery directly,
the turbine could be selected simply to match the load.
In this case, high turbine torque at low speeds would
facilitate starting any machinery, even when it is fully
loaded.
Hydropower: electrical vs. mechanical 197