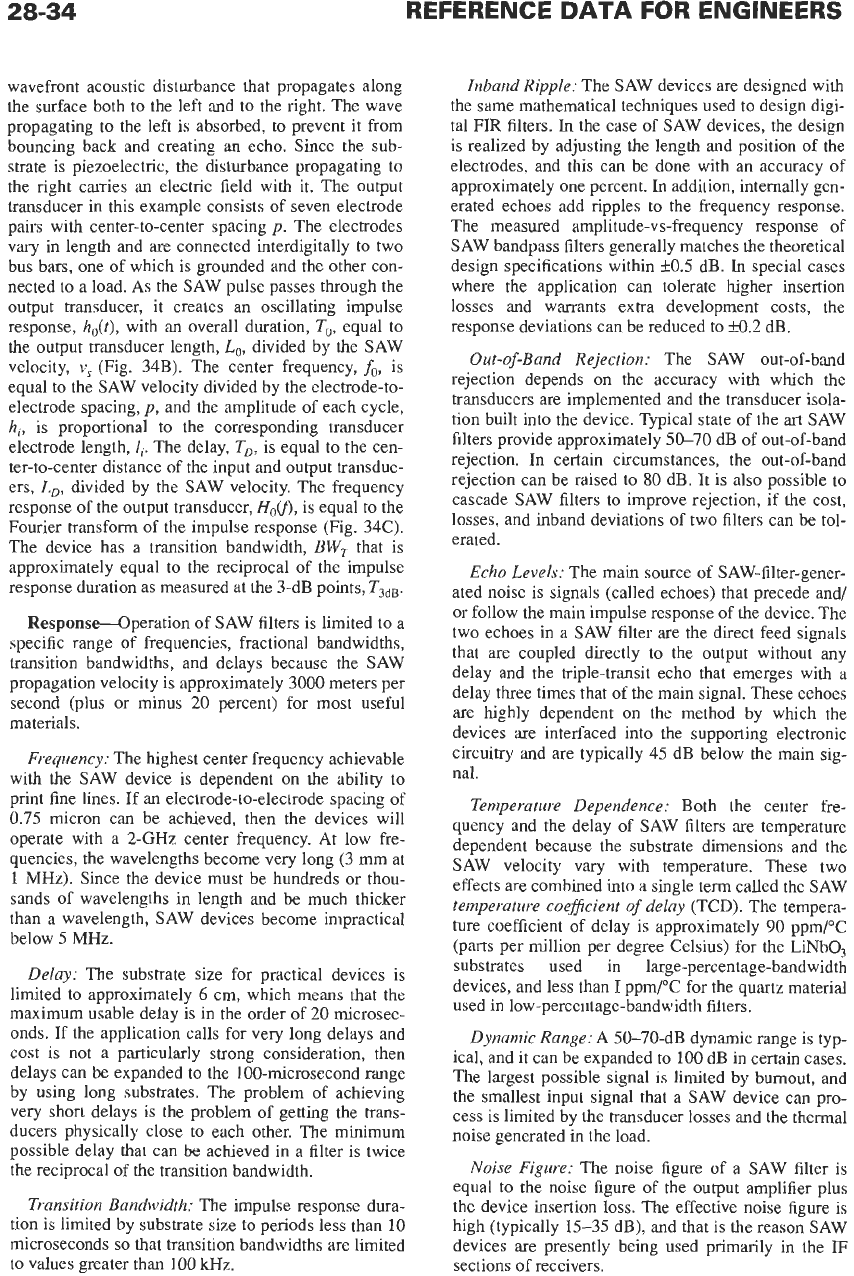
wavefront acoustic disturbance that propagates along
the surface both to the left and to the right. The wave
propagating to the left is absorbed, to prevent it from
bouncing back and creating an echo. Since the sub-
strate is piezoelectric, the disturbance propagating to
the right carries an electric field with it. The output
transducer in this example consists of seven electrode
pairs with center-to-center spacing
p.
The electrodes
vary in length and are connected interdigitally to two
bus bars, one of which is grounded and the other con-
nected
to
a load. As the SAW pulse passes through the
output transducer, it creates an oscillating impulse
response,
h,(t),
with an overall duration,
To,
equal to
the output transducer length,
Lo,
divided by the SAW
velocity,
v,
(Fig. 34B). The center frequency,
fo,
is
equal to the SAW velocity divided by the electrode-to-
electrode spacing,
p,
and the amplitude
of
each cycle,
hi,
is proportional to the corresponding transducer
electrode length,
1,.
The delay,
T,,
is equal to the cen-
ter-to-center distance of the input and output transduc-
ers,
Lo,
divided by the SAW velocity. The frequency
response of the output transducer,
Horn,
is equal to the
Fourier transform of the impulse response (Fig. 34C).
The device has a transition bandwidth,
BW,
that is
approximately equal to the reciprocal of the impulse
response duration as measured at the 3-dB points,
T3dB.
Response-Operation of SAW filters is limited to a
specific range of frequencies, fractional bandwidths,
transition bandwidths, and delays because the SAW
propagation velocity is approximately 3000 meters per
second (plus or minus
20
percent) for most useful
materials.
Frequency:
The highest center frequency achievable
with the SAW device is dependent on the ability to
print fine lines. If an electrode-to-electrode spacing of
0.75 micron can be achieved, then the devices will
operate with a 2-GHz center frequency. At low fre-
quencies, the wavelengths become very long
(3
nun
at
1
MHz).
Since the device must be hundreds or thou-
sands of wavelengths in length and be much thicker
than a wavelength, SAW devices become impractical
below 5 MHz.
Delay:
The substrate size for practical devices is
limited to approximately
6
cm, which means that the
maximum usable delay is in the order of
20
microsec-
onds. If the application calls for very long delays and
cost is not a particularly strong consideration, then
delays can be expanded to the 100-microsecond range
by using long substrates. The problem of achieving
very short delays is the problem of getting the trans-
ducers physically close
to
each other. The minimum
possible delay that can be achieved in a filter is twice
the reciprocal of the transition bandwidth.
Transition Bandwidth:
The impulse response dura-
tion is limited by substrate size to periods less than
10
microseconds
so
that transition bandwidths are limited
to values greater than 100 kHz.
Inband Ripple:
The SAW devices
are
designed with
the same mathematical techniques used to design digi-
tal FIR filters.
In
the case of SAW devices, the design
is realized by adjusting the length and position of the
electrodes, and this can be done with an accuracy of
approximately one percent.
In
addition, internally gen-
erated echoes add ripples to the frequency response.
The measured amplitude-vs-frequency response of
SAW bandpass filters generally matches the theoretical
design specifications within k0.5 dB.
In
special cases
where the application can tolerate higher insertion
losses and warrants extra development costs, the
response deviations can be reduced to
50.2
dB.
Out-of-Band Rejection:
The SAW out-of-band
rejection depends on the accuracy with which the
transducers
are
implemented and the transducer isola-
tion built into the device. Typical state of the
art
SAW
filters provide approximately
50-70
dB of out-of-band
rejection. In certain circumstances, the out-of-band
rejection can be raised
to
80
dB. It
is
also possible to
cascade SAW filters to improve rejection, if the cost,
losses, and inband deviations of two filters can be tol-
erated.
Echo Levels:
The main source
of
SAW-filter-gener-
ated noise is signals (called echoes) that precede and/
or follow the main impulse response of the device. The
two echoes in a SAW filter are the direct feed signals
that are coupled directly to the output without any
delay and the triple-transit echo that emerges with a
delay three times that of the main signal. These echoes
are highly dependent on the method by which the
devices are interfaced into the supporting electronic
circuitry and are typically 45 dB below the main sig-
nal.
Temperature Dependence:
Both the center fre-
quency and the delay of SAW filters
are
temperature
dependent because the substrate dimensions and the
SAW velocity vary with temperature. These two
effects
are
combined into a single term called the SAW
temperature coeflcient
of
delay
(TCD). The tempera-
ture coefficient
of
delay is approximately
90
ppm/”C
(parts per million per degree Celsius) for the LiNbO,
substrates used in large-percentage-bandwidth
devices, and less than
I
ppm/”C for the quartz material
used in low-percentage-bandwidth filters.
Dynamic Range:
A 50-70-dB dynamic range is typ-
ical, and it can be expanded to
100
dB in certain cases.
The largest possible signal
is
limited by burnout, and
the smallest input signal that a SAW device can pro-
cess is limited by the transducer losses and the thermal
noise generated in the load.
Noise Figure:
The noise figure of a SAW filter is
equal to the noise figure of the output amplifier plus
the device insertion loss. The effective noise figure is
high (typically 15-35 dB), and that
is
the reason SAW
devices
are
presently being used primarily in the
IF
sections of receivers.