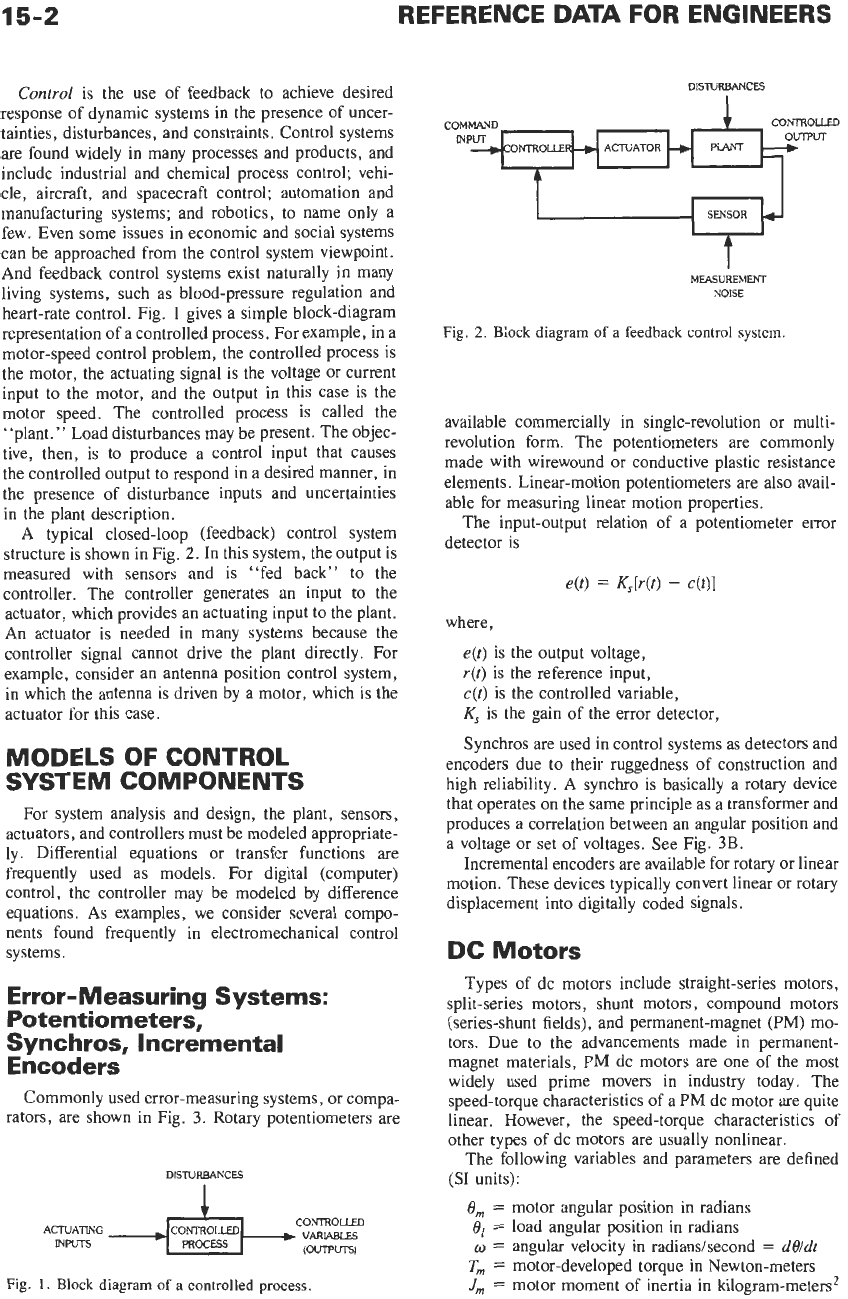
15-2
REFERENCE DATA FOR ENGINEERS
Control
is the use of feedback to achieve desired
response of dynamic systems in the presence of uncer-
tainties, disturbances, and constraints. Control systems
are found widely in many processes and products, and
include industrial and chemical process control; vehi-
cle, aircraft, and spacecraft control; automation and
manufacturing systems; and robotics, to name only a
few. Even some issues in economic and social systems
can be approached from the control system viewpoint.
And feedback control systems exist naturally in many
living systems, such as blood-pressure regulation and
heart-rate control. Fig.
1
gives a simple block-diagram
representation of a controlled process. For example, in a
motor-speed control problem, the controlled process is
the motor, the actuating signal is the voltage or current
input to the motor, and the output in this case is the
motor speed. The controlled process is called the
“plant.” Load disturbances may be present. The objec-
tive, then, is to produce a control input that causes
the controlled output to respond in a desired manner, in
the presence of disturbance inputs and uncertainties
in the plant description.
A
typical closed-loop (feedback) control system
structure is shown in Fig.
2.
In this system, the output is
measured with sensors and is “fed back” to the
controller. The controller generates an input to the
actuator, which provides an actuating input to the plant.
An actuator is needed in many systems because the
controller signal cannot drive the plant directly. For
example, consider an antenna position control system,
in which the antenna is driven by a motor, which is the
actuator for this case.
MODELS
OF
CONTROL
SYSTEM COMPONENTS
For system analysis and design, the plant, sensors,
actuators, and controllers must be modeled appropriate-
ly. Differential equations or transfer functions are
frequently used as models. For digital (computer)
control, the controller may be modeled by difference
equations.
As
examples, we consider several compo-
nents found frequently in electromechanical control
systems.
Error- Measuring Systems:
Potentiometers,
Synchros, Incremental
Encoders
Commonly used error-measuring systems, or compa-
rators, are shown in Fig.
3.
Rotary potentiometers are
DISTURBANCES
CONTROLLED
(OVTPUTSI
ACTUATING
CONTROLLED
INPUTS
PROCESS
Fig.
1.
Block diagram
of
a controlled process.
DISTURBANCES
1
CONTROLLED
COMMAND
t
MEASUREMENT
NOISE
Fig.
2.
Biock diagram
of
a feedback control
system.
available commercially in single-revolution or multi-
revolution form. The potentiometers are commonly
made with wirewound or conductive plastic resistance
elements. Linear-motion potentiometers are also avail-
able for measuring linear motion properties.
The input-output relation of a potentiometer error
detector is
4)
=
W(t)
-
c@)l
where,
e@)
is the output voltage,
r(t)
is the reference input,
c(t)
is the controlled variable,
K,
is the gain of the error detector,
Synchros are used in control systems as detectors and
encoders due to their ruggedness of construction and
high reliability. A synchro is basically a rotary device
that operates on the same principle as a transformer and
produces a correlation between an angular position and
a voltage
or
set of voltages. See Fig.
3B.
Incremental encoders are available for rotary or linear
motion. These devices typically convert linear or rotary
displacement into digitally coded signals.
DC Motors
Types
of
dc motors include straight-series motors,
split-series motors, shunt motors, compound motors
(series-shunt fields), and permanent-magnet (PM) mo-
tors. Due to the advancements made in permanent-
magnet materials,
PM
dc motors are one
of
the most
widely used prime movers in industry today. The
speed-torque characteristics of a
PM
dc motor are quite
linear. However, the speed-torque characteristics of
other types of dc motors are usually nonlinear.
The following variables and parameters are defined
(SI
units):
Om
=
motor angular position in radians
O1
=
load angular position in radians
o
=
angular velocity in radiandsecond
=
dO/dt
Tm
=
motor-developed torque in Newton-meters
Jm
=
motor moment of inertia in kilogram-meters*