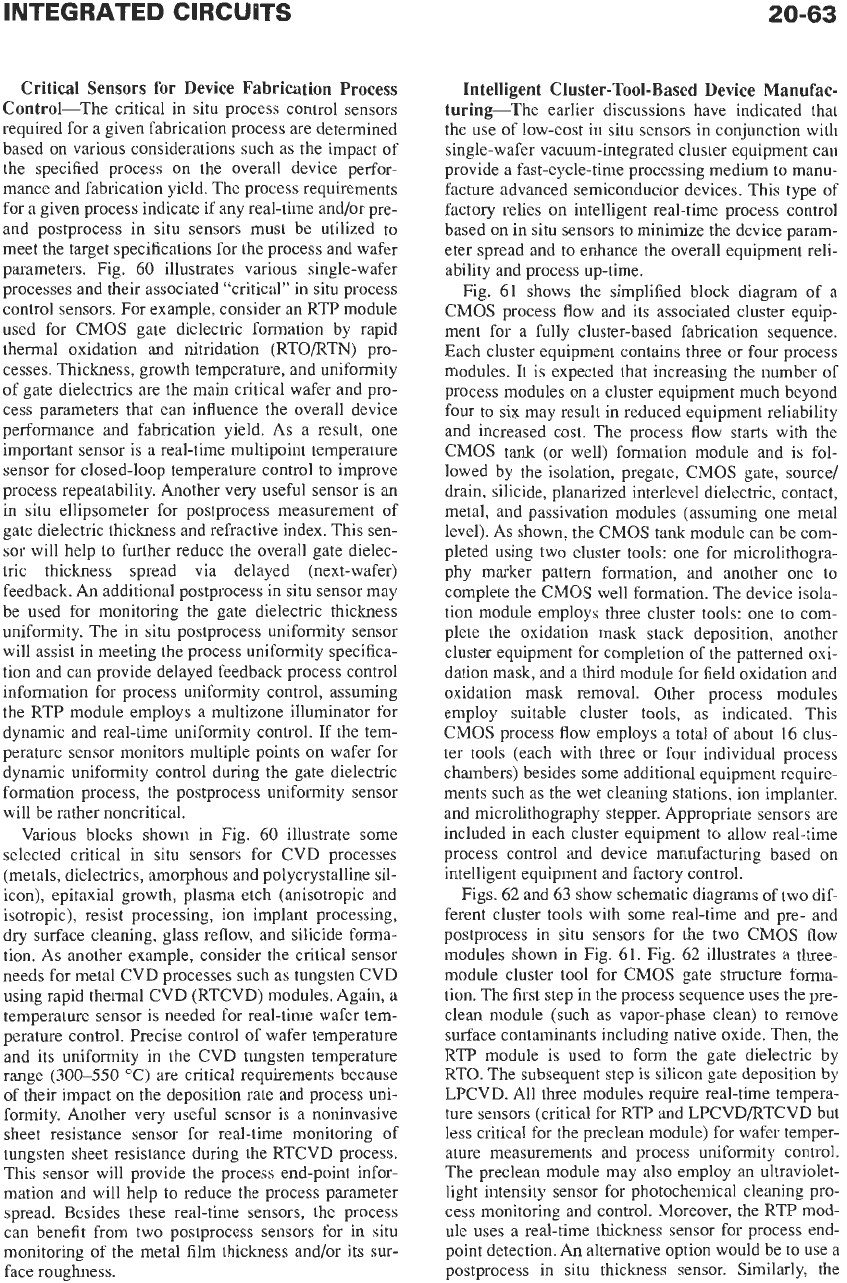
20-63
Critical Sensors for Device Fabrication Process
Control-The critical in situ process control sensors
required for a given fabrication process
are
determined
based on various considerations such as the impact of
the specified process on the overall device perfor-
mance and fabrication yield. The process requirements
for a given process indicate if any real-time and/or pre-
and postprocess in situ sensors must be utilized to
meet the target specifications for the process and wafer
parameters. Fig. 60 illustrates various single-wafer
processes and their associated “critical” in situ process
control sensors. For example, consider an RTP module
used for CMOS gate dielectric formation by rapid
thermal oxidation and nitridation (RTO/RTN) pro-
cesses. Thickness, growth temperature, and uniformity
of gate dielectrics are the main critical wafer and pro-
cess parameters that can influence the overall device
performance and fabrication yield. As a result, one
important sensor is a real-time multipoint temperature
sensor for closed-loop temperature control to improve
process repeatability. Another very useful sensor is an
in situ ellipsometer for postprocess measurement of
gate dielectric thickness and refractive index. This sen-
sor will help to further reduce the overall gate dielec-
tric thickness spread via delayed (next-wafer)
feedback. An additional postprocess in situ sensor may
be used for monitoring the gate dielectric thickness
uniformity. The in situ postprocess uniformity sensor
will assist in meeting the process uniformity specifica-
tion and can provide delayed feedback process control
information for process uniformity control, assuming
the RTP module employs a multizone illuminator for
dynamic and real-time uniformity control. If the tem-
perature sensor monitors multiple points on wafer for
dynamic uniformity control during the gate dielectric
formation process, the postprocess uniformity sensor
will be rather noncritical.
Various blocks shown in Fig. 60 illustrate some
selected critical in situ sensors for CVD processes
(metals, dielectrics, amorphous and polycrystalline sil-
icon), epitaxial growth, plasma etch (anisotropic and
isotropic
j,
resist processing, ion implant processing,
dry surface cleaning, glass reflow, and silicide forma-
tion. As another example, consider the critical sensor
needs for metal CVD processes such as tungsten CVD
using rapid thermal CVD (RTCVD) modules. Again, a
temperature sensor is needed for real-time wafer tem-
perature control. Precise control of wafer temperature
and its uniformity in the CVD tungsten temperature
range (300-550
“C)
are critical requirements because
of their impact on the deposition rate and process uni-
formity. Another very useful sensor is a noninvasive
sheet resistance sensor for real-time monitoring of
tungsten sheet resistance during the RTCVD process.
This sensor will provide the process end-point infor-
mation and will help to reduce the process parameter
spread. Besides these real-time sensors, the process
can benefit from two postprocess sensors for
in
situ
monitoring of the metal film thickness and/or its sur-
face roughness.
Intelligent Cluster-Tool-Based Device Manufac-
turing-The earlier discussions have indicated that
the use of low-cost in situ sensors in conjunction with
single-wafer vacuum-integrated cluster equipment can
provide a fast-cycle-time processing medium to manu-
facture advanced semiconductor devices. This type of
factory relies on intelligent real-time process control
based on in situ sensors to minimize the device param-
eter spread and to enhance the overall equipment reli-
ability and process up-time.
Fig. 61 shows the simplified block diagram
of
a
CMOS process flow and its associated cluster equip-
ment for a fully cluster-based fabrication sequence.
Each cluster equipment contains three or four process
modules.
It
is expected that increasing the number of
process modules on a cluster equipment much beyond
four to six may result in reduced equipment reliability
and increased cost. The process flow starts with the
CMOS tank (or well) formation module and is fol-
lowed by the isolation, pregate, CMOS gate, source/
drain, silicide, planarized interlevel dielectric, contact,
metal, and passivation modules (assuming one metal
level). As shown, the CMOS tank module can be com-
pleted using two cluster tools: one for microlithogra-
phy marker pattern formation, and another one to
complete the CMOS well formation. The device isola-
tion module employs three cluster tools: one to com-
plete the oxidation mask stack deposition, another
cluster equipment for completion of the patterned oxi-
dation mask, and a third module for field oxidation and
oxidation mask removal. Other process modules
employ suitable cluster tools, as indicated. This
CMOS process flow employs a total of about
16
clus-
ter tools (each with three or four individual process
chambers) besides some additional equipment require-
ments such as the wet cleaning stations, ion implanter,
and microlithography stepper. Appropriate sensors are
included in each cluster equipment to allow real-time
process control and device manufacturing based on
intelligent equipment and factory control.
Figs. 62 and 63 show schematic diagrams of two dif-
ferent cluster tools with some real-time and pre- and
postprocess in situ sensors for the two CMOS flow
modules shown
in
Fig.
61.
Fig. 62 illustrates a three-
module cluster tool for CMOS gate structure forma-
tion. The first step in the process sequence uses the pre-
clean module (such as vapor-phase clean)
to
remove
surface contaminants including native oxide. Then, the
RTP module is used to form the gate dielectric by
RTO. The subsequent step
is
silicon gate deposition
by
LPCVD. All three modules require real-time tempera-
ture sensors (critical for RTP and LPCVDBTCVD but
less critical for the preclean module) for wafer temper-
ature measurements and process uniformity control.
The preclean module may also employ an ultraviolet-
light intensity sensor for photochemical cleaning pro-
cess monitoring and control. Moreover, the RTP mod-
ule uses a real-time thickness sensor for process end-
point detection. An alternative option would be to use a
postprocess in situ thickness sensor. Similarly, the