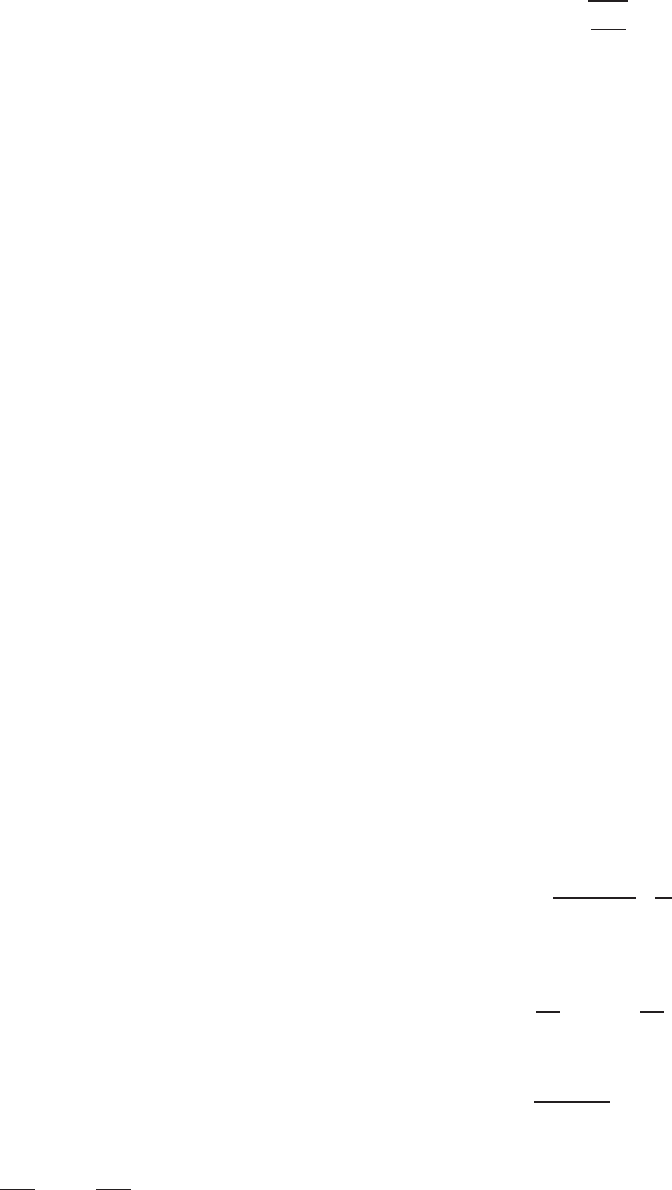
142 4 FLEXURAL MEMBERS
This model was subsequently improved to include more
consistent treatment of the web. Their model is used in
the Standards of A ustralia and New Zealand.
1.391
In 1999,
Schafer and Pekoz further developed the model to allow
for the impact of applied stresses on the web’s rotational
stiffness, thus allowing for the case when distortional buck-
ling is triggered by instability of the web as opposed to the
flange.
3.168
Schafer and Pekoz’s model is used in the North
American Specification.
1.345
4.2.4.2 North American Design Criteria for Distortional
Buckling Strength of Open-Section Flexural Members
In the North American Specification, Appendix 1 was
developed in 2004 for the use of the direct-strength method
to determine the structural strength of cold-formed steel
members by considering local buckling, distortional buck-
ling, and overall (global) buckling.
1.343
Subsequently, in
2007, a new Section C3.1.4 was added to the main
document of the North American Specification for deter-
mining the distortional buckling strength of I-, Z-, C-, and
other open cross-sectional flexural members having edge-
stiffened compression flanges.
1.345
For the convenience of readers, the following excerpts
are adapted from the 2007 edition of the North Amer-
ican Specification.
4.228
At the present time (2009), the
AISI Committee intends to move Section C3.1.4(a) to the
Commentary because it is for preliminary design and has
been specifically derived to always be more conservative
than Section C3.1.4(b).
C3.1.4 Distortional Buckling Strength [Resistance]
The provisions of Section C3.1.4 of the specification shall
apply to I-, Z-, C-, and other open cross-section members
that employ compression flanges with edge stiffeners, with
the exception of members that meet the criteria of Sections
4.2.5 and 4.2.6 w hen the R factor of Eq. (4.123) is employed
or Section 4.2.6.1. The nominal flexural strength [moment
resistance] shall be calculated in accordance with Eq. (4.104)
or Eq. (4.105). The safety factor and resistance factors given in
this section of the specification shall be used to determine the
allowable flexural strength or design flexural strength [factored
moment resistance] in accordance with the applicable design
method in Section 3.3.1, 3.3.2, or 3.3.3:
b
= 1.67 (ASD)
φ
b
=
0.90 (LRFD)
0.85 (LSD)
For λ
d
≤ 0.673
M
n
= M
y
(4.104)
For λ
d
> 0.673
M
n
=
1 − 0.22
M
crd
M
y
0.5
M
crd
M
y
0.5
M
y
(4.105)
where
λ
d
=
M
y
M
crd
(4.106)
M
y
= S
fy
F
y
(4.107)
where S
fy
is the elastic section modulus of full unreduced
section relative to the extreme fiber in the first yield and
M
crd
= S
f
F
d
(4.108)
where S
f
= elastic section modulus of full unreduced section
relative to extreme compression fiber
F
d
= elastic distortional buckling stress calculated in
accordance with either Section C3.1.4(a), (b), or
(c)
(a) Simplified Provision for Unrestrained C- and Z-Sections
with Simple Lip Stiffeners. For C- and Z-sections that have no
rotational restraint of the compression flange and are within the
dimensional limits provided in this section of the specification,
Eq. (4.109) shall be permitted to be used to calculate a
conservative prediction of the distortional buckling stress, F
d
.
See Section C3.1.4(b) or C3.1.4(c) for alternative provisions
and for members outside the dimensional limits of this section.
The following dimensional limits shall apply:
1. 50 ≤ h
o
/t ≤ 200,
2. 25 ≤ b
o
/t ≤ 100,
3. 6.25 < D /t ≤ 50,
4. 45
◦
≤ θ<90
◦
,
5. 2 ≤ h
o
/b
o
≤ 8, and
6. 0.04 ≤ D sinθ /b
o
≤ 0.5.
where h
o
=out-to-out web depth as defined in Fig. 3.30c
t = base steel thickness
b
o
= out-to-out flange width as d efined in Fig. 3.30c
D = out-to-out lip dimension as defined in Fig. 3.48
θ = lip angle as defined in Fig. 3.48
The distortional buckling stress F
d
shall be calculated as
follows:
F
d
= βk
d
π
2
E
12(1 − μ
2
)
t
b
o
2
(4.109)
where β, a value accounting for the moment gradient, which
is permitted to be conservatively taken as 1.0, is given as
β = 1.0 ≤ 1 + 0.4
L
L
m
0.7
1 +
M
1
M
2
0.7
≤ 1.3 (4.110)
where L is the minimum of L
cr
and L
m
:
L
cr
= 1.2h
o
b
o
Dsin θ
h
o
t
0.6
≤ 10h
o
(4.111)
L
m
is the distance between discrete restraints that restrict
distortional buckling (for continuously restrained members
L
m
= L
cr
); M
1
and M
2
are the smaller and the larger end
moments, respectively, in the unbraced segment (L
m
)ofthe