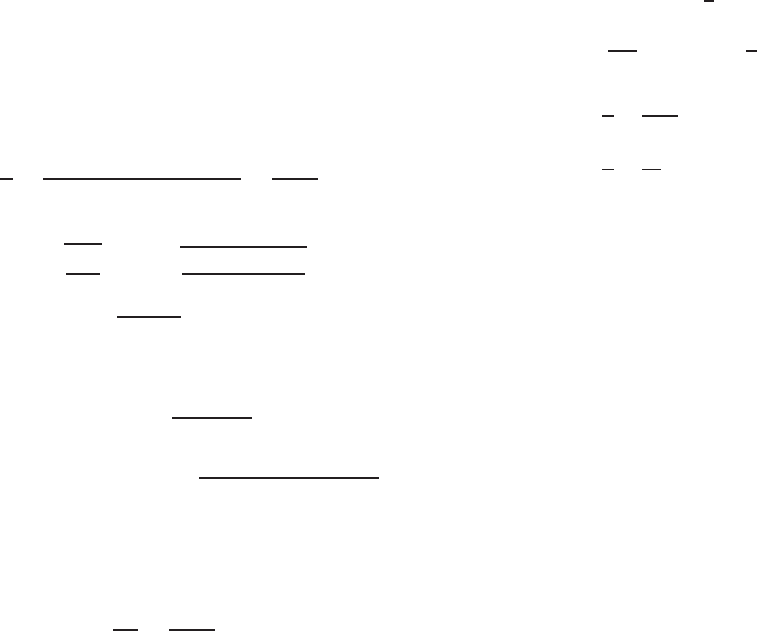
DESIGN OF BEAM WEBS 165
B. LRFD Method.
Based on the same nominal shear strength computed in item
A, the design shear strength using the LRFD method for
the design of the channel section is
φ
v
V
n
= (0.95)(6.22) = 5.91 kips
Example 4.20 Use the ASD and LRFD methods to deter-
mine the available shear strength for the hat section used
in Example 4.3. Use F
y
= 50 ksi.
SOLUTION
A. ASD Method.
The depth-to-thickness ratio of the web is
h
t
=
10 − 2
(
0.105 + 0.1875
)
0.105
=
9.415
0.105
= 89.67
Based on k
v
= 5.34 and F
y
= 50 ksi,
1.51
Ek
v
F
y
= 1.51
(29,500)(5.34)
50
= 84.76
Since h/t > 1.51
Ek
v
/F
y
, use Eq. (4.157c) to c ompute
the nominal shear strength, V
n
, for the hat section having
two webs a s follows:
V
n
= A
w
F
v
= 2(ht)
0.904Ek
v
(h/t)
2
= 2(9.415 × 0.105)
0.904 × 29500 ×5.34
(89.67)
2
= 35.02 kips
The allowable shear strength using the ASD method for the
design of the hat section is
V
a
=
V
n
v
=
35.02
1.60
= 21.89 kips
B. LRFD Method.
Based on the same nominal shear strength computed in item
A, the design shear strength using the LRFD method for
the design of the hat section is
φ
v
V
n
= (0.95)(35.02) = 33.27 kips
4.3.3.3 Shear Strength of C-Section Webs with Holes
When holes are present in beam webs, the effect of web
perforation on the reduction of shear strength of C-sections
was investigated in the 1990s by Shan et al.,
3.184,3.197
Schuster et al.,
3.187
and Eiler.
3.192
In these s tudies, three
hole geometries (rectangular hole with corner fillets,
circular hole, and diamond-shaped hole) were considered
in the test programs. Based on the results of research
findings, Section C3.2.2 was added in the supplement to
the 1996 edition of the AISI Specification in 1999
1.333
and
is retained in the North American Specification.
1.336,1.345
Based on Section C3.2.2 of the Specification, for
C-section webs with holes, the shear strength shall be
calculated in accordance with Section C3.2.1, multiplied
by the reduction factor q
s
, a s defined in Eq. (4.160a) or
(4.160b), under the same limits given in Section 3.6.3:
q
s
=
⎧
⎪
⎨
⎪
⎩
1.0when
c
t
≥ 54 (4.160a)
c
54t
when 5 ≤
c
t
< 54 (4.160b)
c =
⎧
⎪
⎪
⎨
⎪
⎪
⎩
h
2
−
d
h
2.83
for circular holes (4.161a)
h
2
−
d
h
2
for noncircular holes (4.161b)
where d
h
= depth of web hole
h = depth of flat portion of web measured along
plane of the web
t = web thickness
Similar to Section B2.4 of the Specification (Section
3.6.3 in this volume), the above design provisions for
circular and noncircular holes apply to any hole pattern
that fits within an equivalent virtual hole, as shown in
Figs. 3.64 a nd 3.65.
4.3.4 Bending
Webs of beams can buckle not only in shear but also due
to the compressive stress caused by bending, for example,
at the location of a maximum moment. Figure 3.27 s hows
a typical pattern of bending failure of beam webs.
The web buckling stress due to bending and the postbuck-
ling strength of flat beam webs are discussed in Section
3.5.1.2. The same section also discusses the AISI design
equations for computing the effective design depth of beam
webs.
For beam webs having relatively large depth-to-thickness
ratios, the buckling of w eb elements becomes more impor-
tant. The structural efficiency of such beam webs can be
improved by adding longitudinal stiffeners in the compres-
sion portion of the web, as shown in Fig. 4.59. References
4.60, 4.65, and 4.66 present the studies made by Nguyen
and Yu on the structural behavior of longitudinally rein-
forced beam webs.
In Europe, the design methods for profiled sheeting and
sections with stiffeners in the flanges and webs are provided
in Refs. 1.209 and 3.56.
The DSM provided in Appendix 1 of the North American
Specification can handle the available bending strength of
beams having longitudinal web stiffeners.