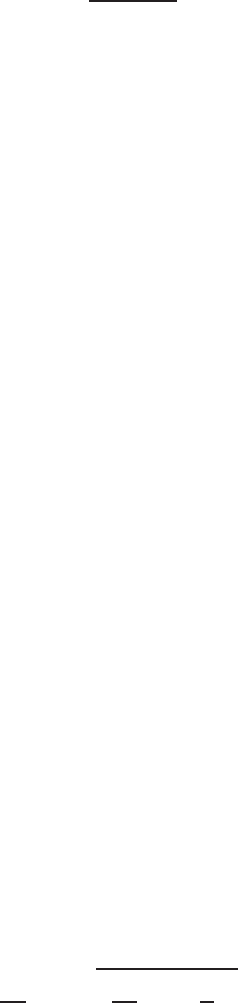
BRACING OF AXIALLY LOADED COMPRESSION MEMBERS 209
The K values to be used for the design of unbraced
multistory or multibay frames can be obtained from the
alignment chart in Fig. 5.23.
1.158
In the chart, G is
defined as
G =
(
I
c
/L
c
)
(
I
b
/L
b
)
(5.75)
in which I
c
is the moment of inertia and L
c
the unbraced
length of the column and I
b
is the moment of inertia and
L
b
the unbraced length of the beam.
In practical design, when a column base is supported by
but not rigidly connected to a footing or foundation, G is
theoretically infinity, but unless actually designed as a true
friction-free pin, it may be taken as 10. If the column end
is rigidly attached to a properly designed footing, G may
be taken as 1.0.
1.158,5.67
In the use of the chart, the beam stiffness I
b
/L
b
should
be multiplied by a factor as follows when the c onditions at
the far end of the beam are known:
1. Sidesway is prevented:
1.5 for far end of beam hinged
2.0 for far end of beam fixed
2. Sidesway is not prevented:
0.5 for far end of beam hinged
0.67 for far end of beam fixed
After determining G
A
and G
B
for joints A and B at two
ends of the column section, the K value can be obtained
from the alignment chart of Fig. 5.23 by constructing a
straight line between the appropriate points on the scales
for G
A
and G
B
.
5.10 BUILT-UP COMPRESSION MEMBERS
For built-up compression members composed of two
sections in contact, the available axial strength (factored
axial resistance) shall be determined in accordance with
Section C4.1(a) of the North American Specification
(Section 5.8 in this volume) subjected to modification as
necessary. Based on Section D1.2 of the 2007 edition of
the North American specification, if the buckling mode
involves relative deformations that produce shear forces in
the connections between individual shapes, the effective
slenderness ratio KL/r is replaced by the modified effective
slenderness ratio (KL/r )
m
calculated by Eq. (5.76):
KL
r
m
=
KL
r
2
0
+
a
r
i
2
(5.76)
where (KL/r)
0
= overall slenderness ratio of entire section
about built-up member axis
a = intermediate fastener or spot weld
spacing
r
i
= minimum radius of gyration of full
unreduced cross-sectional area of an
individual shape in built-up member
See Section 5.8 for definition of other symbols. In addition,
the fastener strength (resistance) and spacing shall satisfy
the following:
1. The intermediate fastener or spot weld spacing a is
limited such that a/r
i
does not exceed one-half the
governing slenderness ratio of the built-up member.
2. The ends of a built-up compression member are
connected by a weld having a length not less than
the maximum width of the member or by connectors
spaced longitudinally not more than four diameters
apart for a distance equal to 1.5 times the maximum
width of the member.
3. The intermediate fastener(s) or weld(s) at any longi-
tudinal member tie location are capable of transmit-
ting a force in any direction of 2.5% of the nominal
axial strength (compressive resistance) of the built-up
member.
In the above design criteria, Eq.(5.76) was added to the
North American Specification since 2001 on the basis of the
1999 AISC Specification and the 1994 CSA Standard.
1.117
The overall slenderness ratio, (KL/r)
0
, is computed about
the same axis as the modified slenderness ratio, (KL/r)
m
.
The (KL/r)
m
ratio replaces KL/r for both flexural and
flexural–torsional buckling.
Section D1.2 of the North American Specification
includes the above three requirements concerning interme-
diate fastener spacing a, end connection of the built-up
member, and the applied force for the design of inter-
mediate fastener(s). The intermediate fastener spacing
requirement (1) for [a/r
i
≤ 0.5(KL/r)] is to prevent
flexural buckling of individual shapes between interme-
diate connectors to account for any one of the connectors
becoming loose or ineffective. Requirements 2 and 3 are
related to connection design as discussed in Section 8.8
and illustrated in Example 8.6.
For the research work on built-up compression
members, recent studies have been made by Yang and
Hancock,
5.188,5.191
Brueggen and Ramseyer,
5.189
Stone and
LaBoube,
5.190
Young and Chen,
5.192
and others.
5.11 BRACING OF AXIALLY LOADED
COMPRESSION MEMBERS
In the 2007 edition of the North American Specification,
new design provisions are included for bracing of axially
loaded compression members. According to Section D3.3