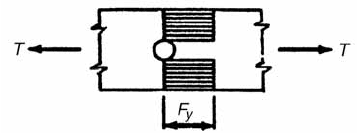
224 6 COMBINED AXIAL LOAD AND BENDING
6.2 COMBINED TENSILE AXIAL LOAD
AND BENDING
6.2.1 Tension Members
For the design of tension members using hot-rolled
steel shapes and built-up members, the AISC Specifi-
cations
1.148,3.150,1.411
provide design provisions for the
following three limit states: (1) yielding of the full section
between connections, (2) fracture of the effective net area
at the connection, and (3) block shear fracture at the
connection.
For cold-formed steel design, Section C2 of the 1996
AISI Specification provided Eq. (6.1) for calculating the
nominal tensile strength of axially loaded tension members,
with a safety factor for the ASD method and a resistance
factor for the LRFD method as follows:
T
n
= A
n
F
y
(6.1)
t
= 1.67 (ASD)
φ
t
= 0.95 (LRFD)
where T
n
= nominal tensile strength
A
n
= net area of the cross section
F
y
= design yield s tress
In addition, the nominal tensile strength was also limited
by Section E.3.2 of the 1996 Specification for tension in
connected parts.
When a tension member has holes, s tress concentration
may result in a higher tensile stress adjacent to a hole to
be about three times the average stress on the net area.
6.36
With increasing load and plastic stress redistribution, the
stress in all fibers on the net area will reach the yield stress,
as shown in Fig. 6.2. Consequently, the AISI specification
has used Eq. (6.1) for determining the maximum tensile
capacity of axially loaded tension members since 1946.
This AISI design approach differs significantly from the
AISC design provisions, which consider yielding of the
gross cross-sectional area, fracture of the effective net area,
and block shear. The reason for not considering the fracture
criterion in the 1996 AISI Specification was mainly due to
the lack of research data relative to the shear lag e ffect on
tensile strength of cold-formed steel members.
Figure 6.2 Stress distribution for nominal tensile strength.
In 1995, the influence of shear lag on the tensile capacity
of bolted connections in cold-formed steel angles and c han-
nels was investigated by Carril, Holcomb, LaBoube, and
Yu at the University of Missouri-Rolla. Design equations
were recommended in R efs. 6.23–6.25 for computing
the effective net area. This design information enables
the consideration of fracture s trength at connections for
angles and channels. The same study also investigated
the tensile strength of staggered bolt patterns in flat-sheet
connections.
On the basis of the results of past research, Section C2 of
the Specification was revised in 1999. This AISI Supple-
ment to the specification included revised provisions for
the design of axially loaded tension members.
1.333
The
same design provisions were included in Section C2 of
Appendix A of the North American Specifications
1.336,1.346
for the design of tension members in the United States and
Mexico. In Canada, the design of tension members has been
based on Appendix B of the 2007 edition of the North
American Specification.
The following design requirements are adapted from
Section C2 of Appendix A of the 2007 edition of the North
American Specification.
C2 Tension Members
For axially loaded tension members, the nominal tensile
strength, T
n
, shall be the smaller value obtained in accor-
dance with the limit states of (a), (b), and (c). Unless otherwise
specified, the corresponding safety factor and resistance factor
provided in this section of the Specification shall be used to
determine the available strengths in accordance with the appli-
cable method in Sections 3.3.1 or 3.3.2.
(a) For yielding in gross section:
T
n
= A
g
F
y
(6.2)
t
= 1.67 (ASD)
φ
t
= 0.90 (LRFD)
where T
n
= nominal strength of member when loaded in
tension
A
g
= gross area o f cross section
F
y
= yield stress as specified in Section A7.1
(b) For rupture in the net section away from connection:
T
n
= A
n
F
u
(6.3)
t
= 2.00 (ASD)
φ
t
= 0.75 (LRFD)
where A
n
= net area o f cross section
F
u
= tensile strength as specified in Section A2.1
or A2.3.2